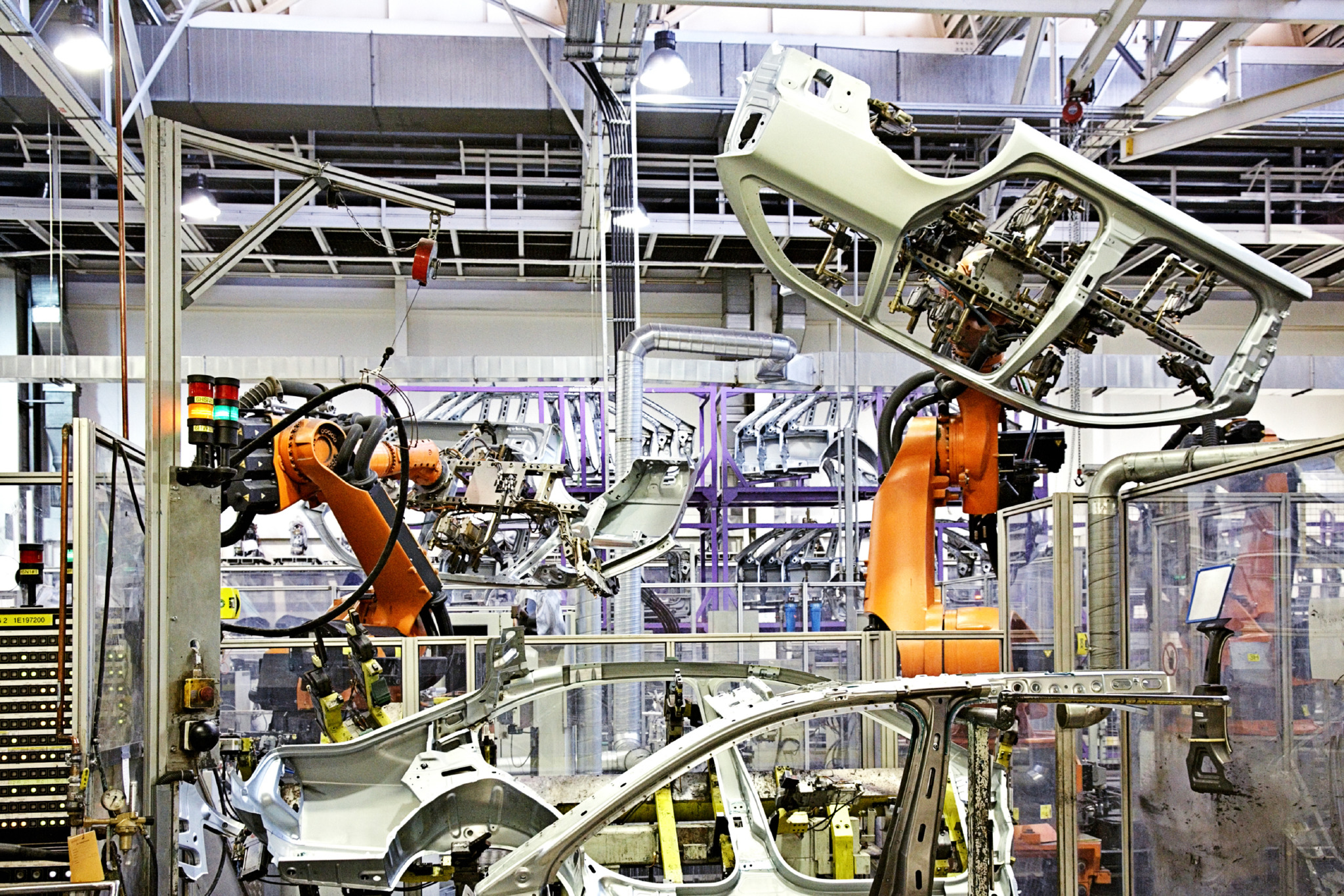
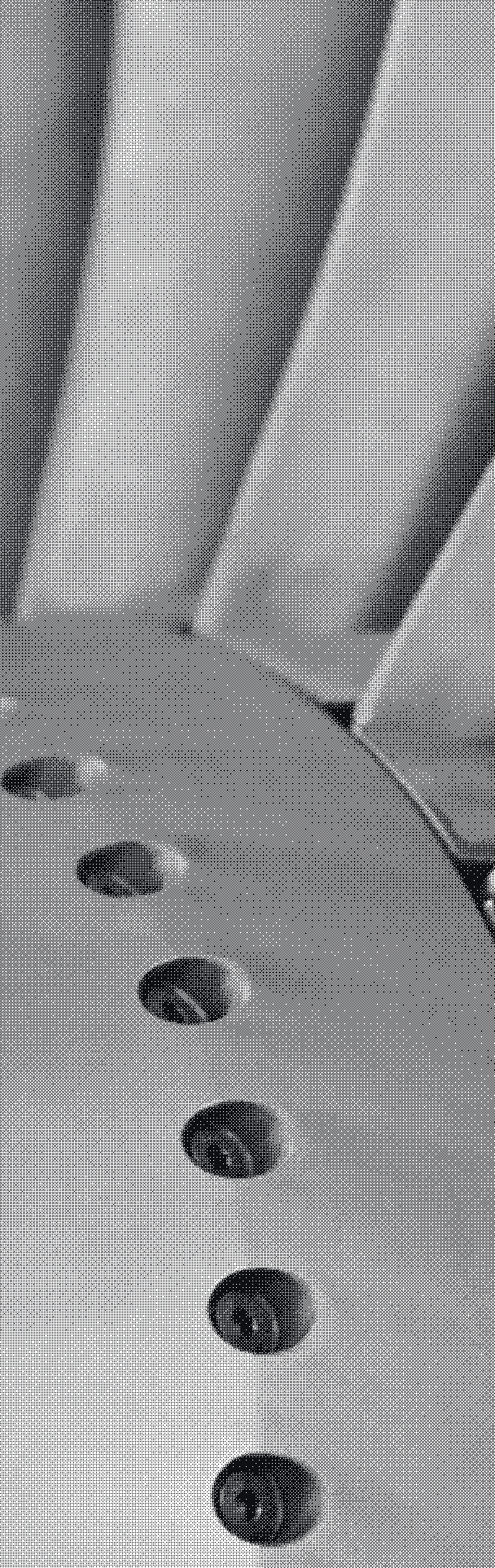
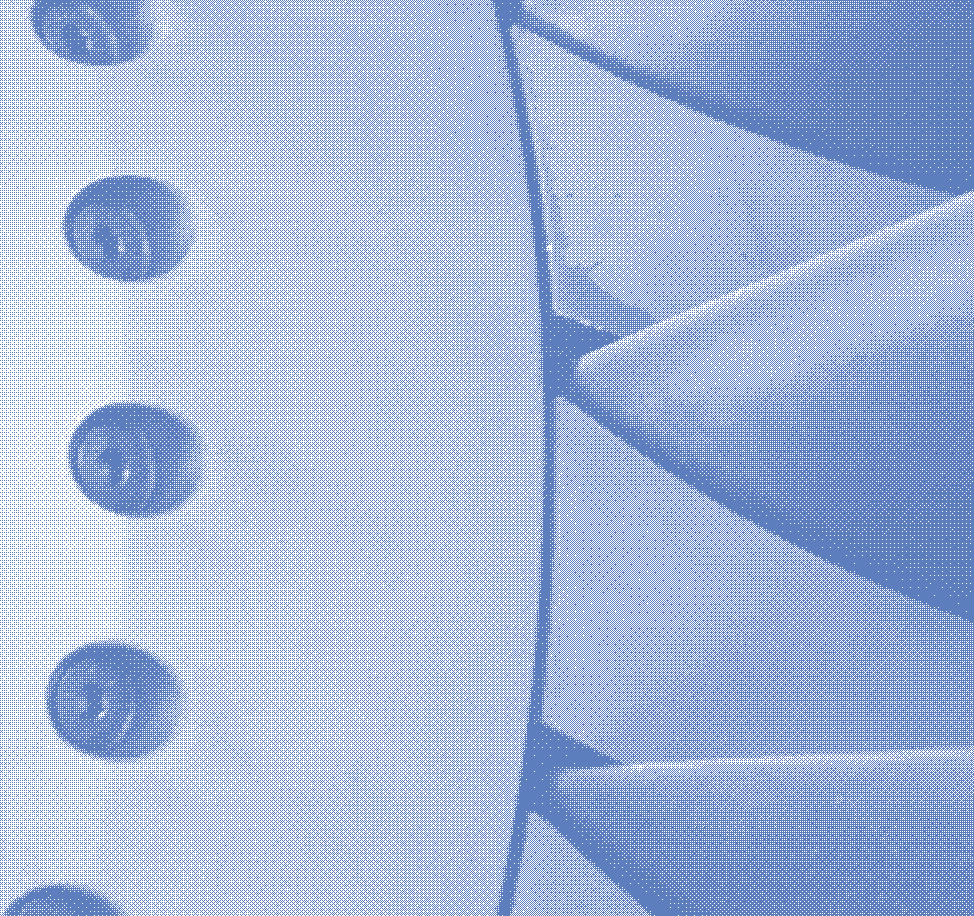
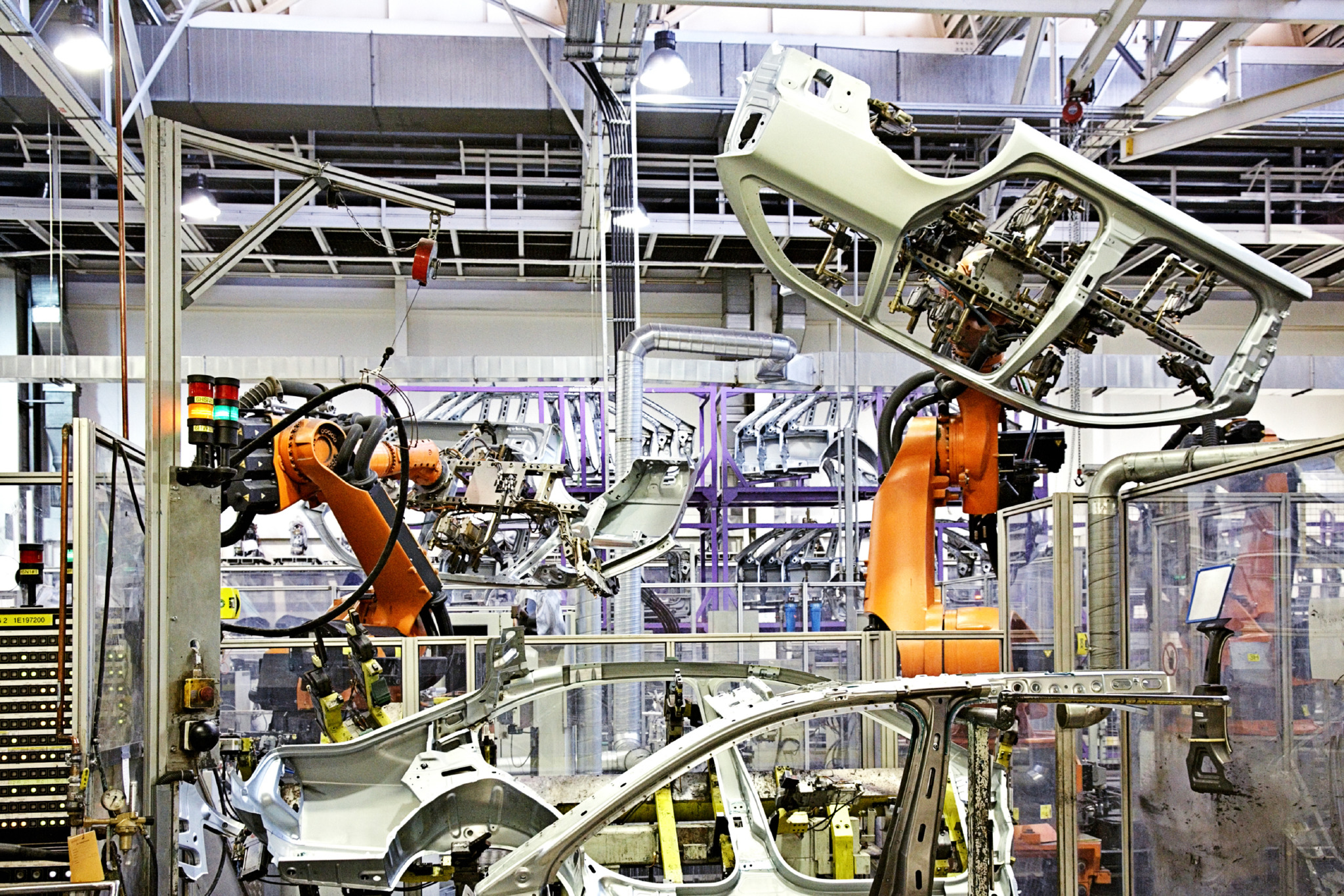
News, Views & Events
Events
LightForm Seminar: Forming and Joining Challenges in Lightweighting of Autobody Structures
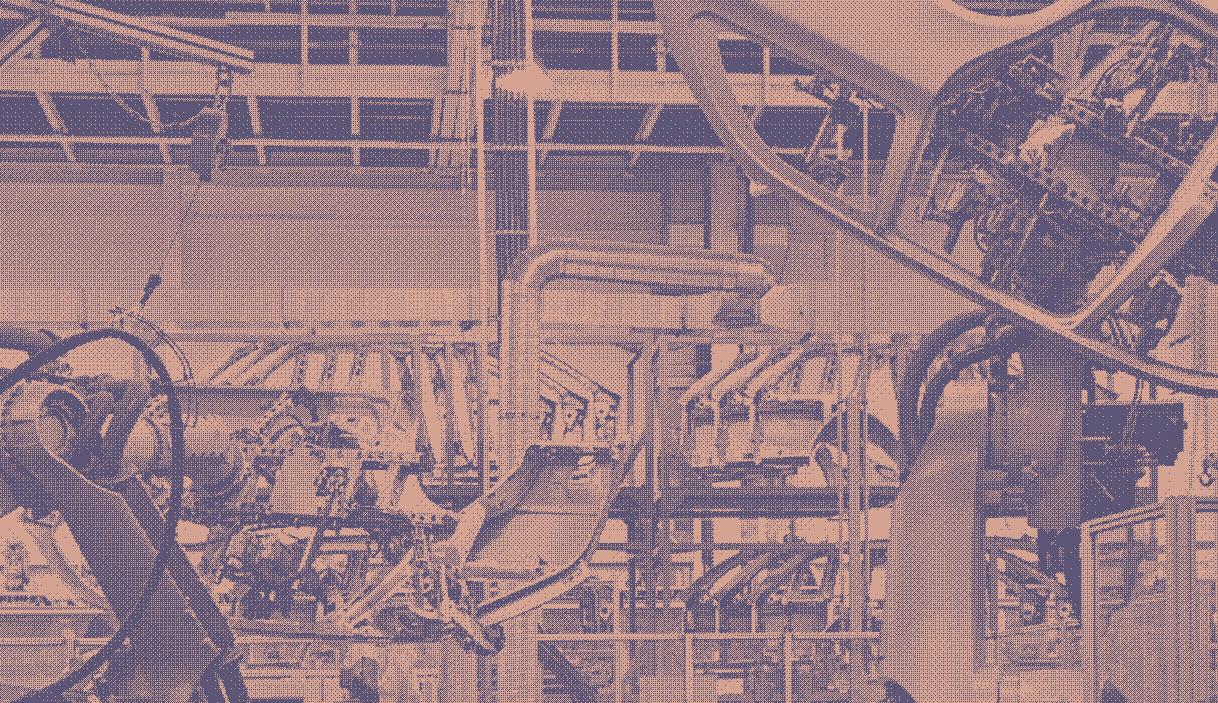
Dr Michael Miles from the Manufacturing Engineering Department, Brigham Young University presented “Forming and Joining Challenges in Lightweighting of Autobody Structures” at The University of Manchester on the 25 March 2019.
Lightweighting of the autobody structure is challenging on several fronts. Advanced high strength steels are less formable than lower carbon alloys that have been used in the past and multi-material strategies that introduce light metals into the structure require the joining of dissimilar alloys.
During the past three years two research projects at Brigham Young University have focused on both forming and joining problems.
The forming project, in collaboration with General Motors and supported by the National Science Foundation, investigated the effect of retained austenite (RA) transformation on material ductility for Q&P 1180 and TRIP 1180 steels. Different strain paths were imposed on sheet specimens, including biaxial tension, plane-strain tension, and uniaxial tension, while electron backscatter diffraction (EBSD) was used to identify phases at various levels of strain until failure. RA transformation rates were found to be a function of both the strain path and the microstructure.
The joining project, in collaboration with Honda / Oak Ridge National Lab and supported by the Department of Energy, focused on a solid state spot joining method for a dissimilar combination of AA7085-T6 and DP 1180. Joints were tested in lap shear tension, cross tension, and t-peel configurations, in order to evaluate strength levels compared to required industry standards. Corrosion testing was also performed in order to evaluate whether various coating/adhesive combinations would allow for adequate protection of the spot joints.