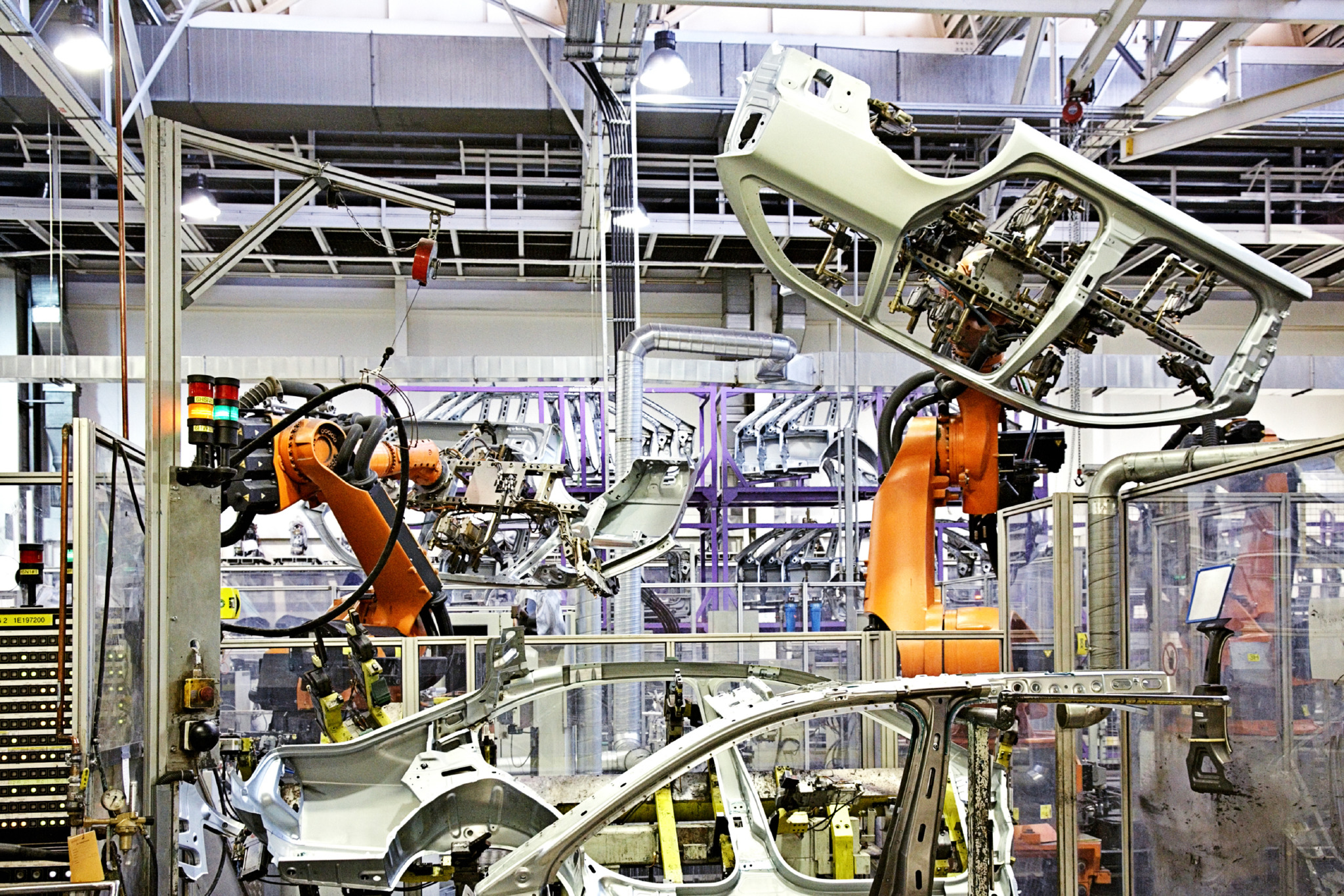
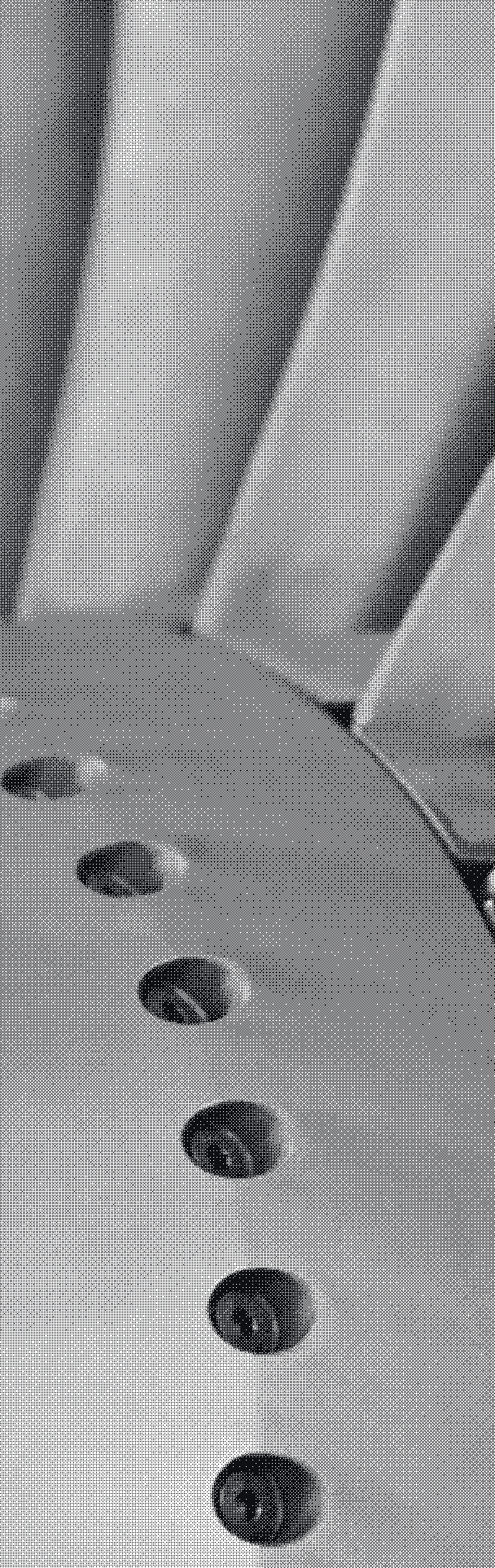
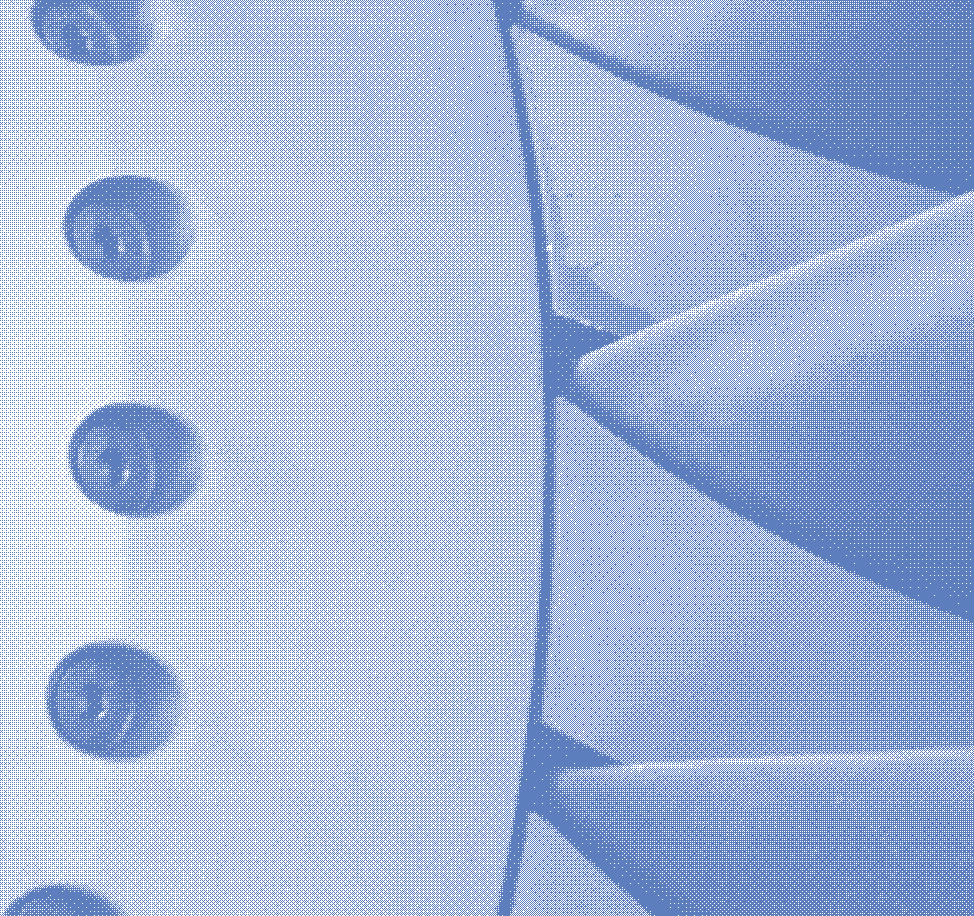
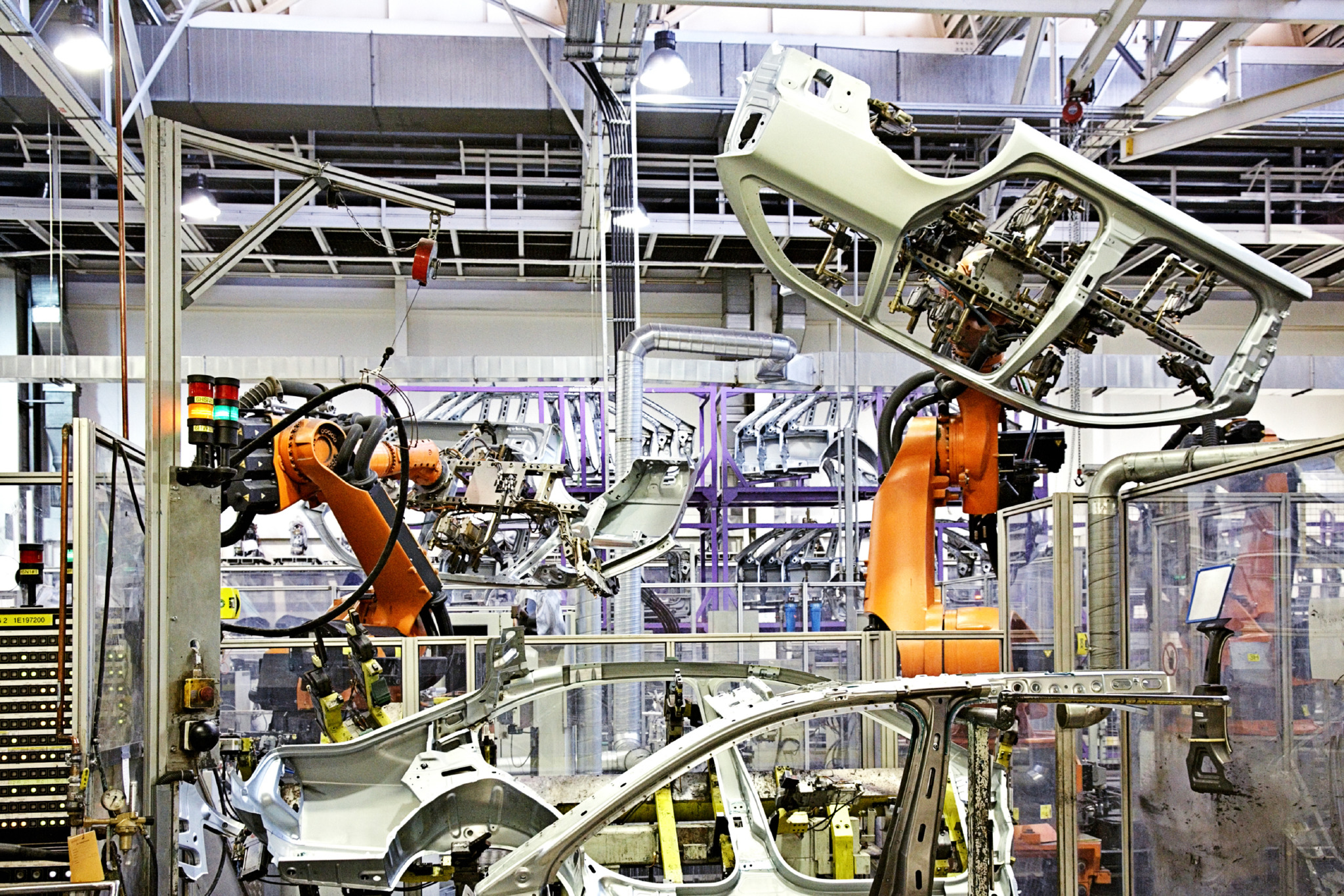
News, Views & Events
News
LightForm watches unstable grain coarsening in titanium aerospace microstructure at 1000 degrees Celsius
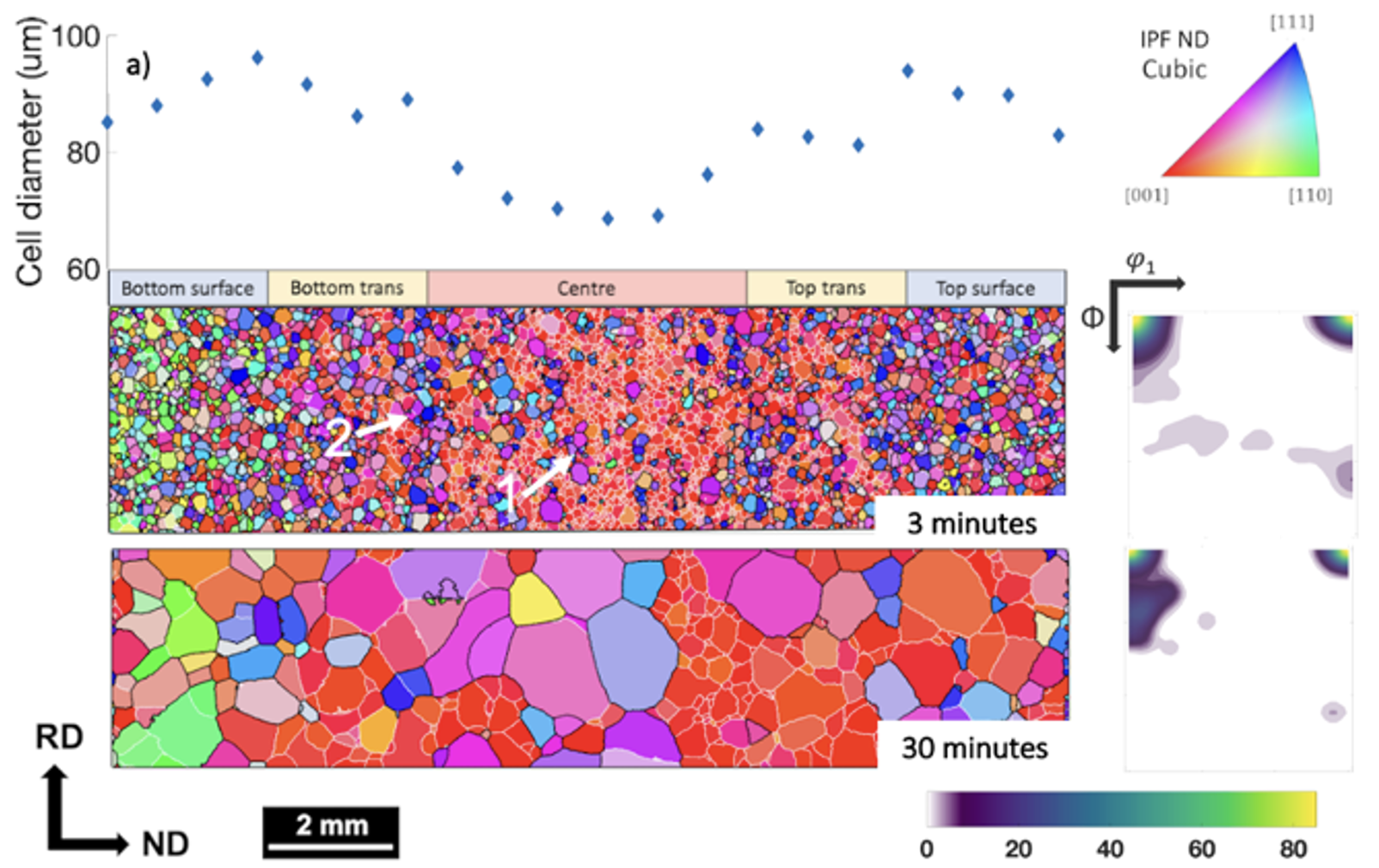
Investigations conducted by the LightForm research team, in collaboration with Airbus, have uncovered a missing link in understanding the origin of detrimental microstructures in damage-tolerant titanium components for the aerospace industry.
When beta-annealing Ti64 wrought products, an unusual unstable coarsening behaviour can cause abnormal coarse grain (ACG) structures to develop intermittently during heat treatments, which can affect performance in-service. Parts found to have such extremely coarse cm – scale grains are therefore rejected, which is costly for high value machined titanium components.
Until recently the origin of this behaviour was the subject of considerable speculation. It has been suggested that strong crystallographic textures developed during processing (i.e. the statistically high probability of a preferred crystal orientation) play a key role in setting up the conditions for the growth of ACGs. However, until now, the mechanism by which this leads to such ‘explosive’ growth of a few grains during annealing had eluded the community. Using a novel, state-of-the-art, high temperature scanning electron microscopy technique with an ultra-clean environment to remove oxygen, combined with electron back scattered diffraction (EBSD) imaging at temperatures up to 1000 °C, the phenomena has been observed as it happened in real time, for the first time.
Using data from these difficult experiments, combined with results obtained from incremental ex-situ annealing studies and large-area EBSD data sets of the starting texture distributions in hot rolled plate, LightForm researchers have successfully described and explained each stage of the annealing process, using a well-established theory that was previously developed in the light alloys group at the University of Manchester.
Nick Byres, PhD candidate and lead researcher on this study said, “After spending so much time wondering how these structures develop inside large forgings at over 1000 °C, it was incredible to actually watch them develop right before our eyes!”
These results will help wrought titanium producers to design more informed and effective processing regimes in order to more consistently produce higher quality products, whilst reducing waste and the unnecessary use of resources throughout the industry.
The experiment data is available on the LightForm Zenodo repository (click here)