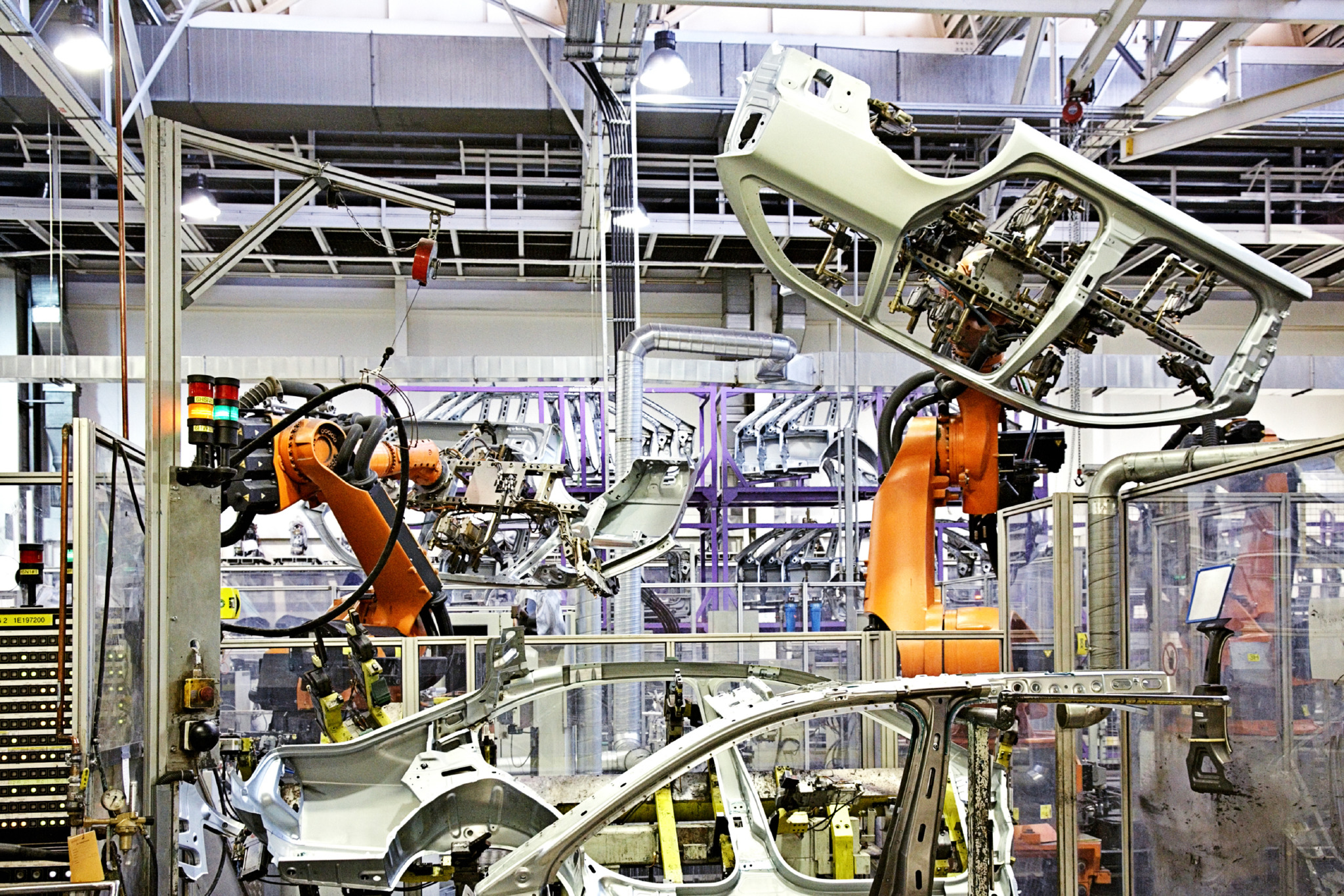
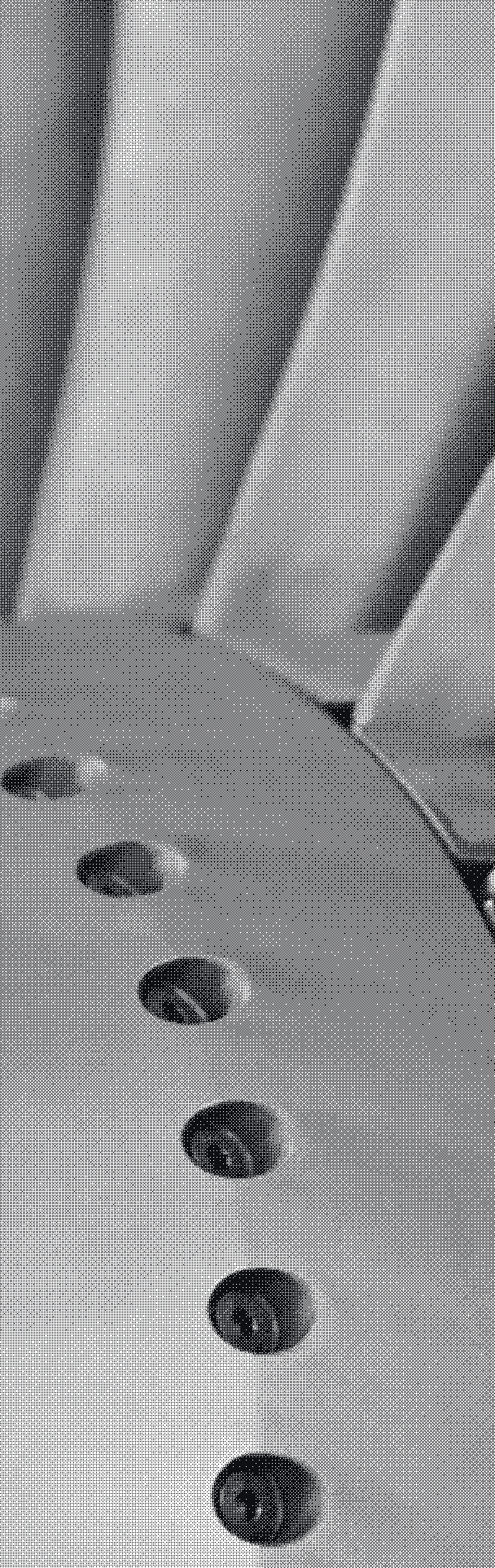
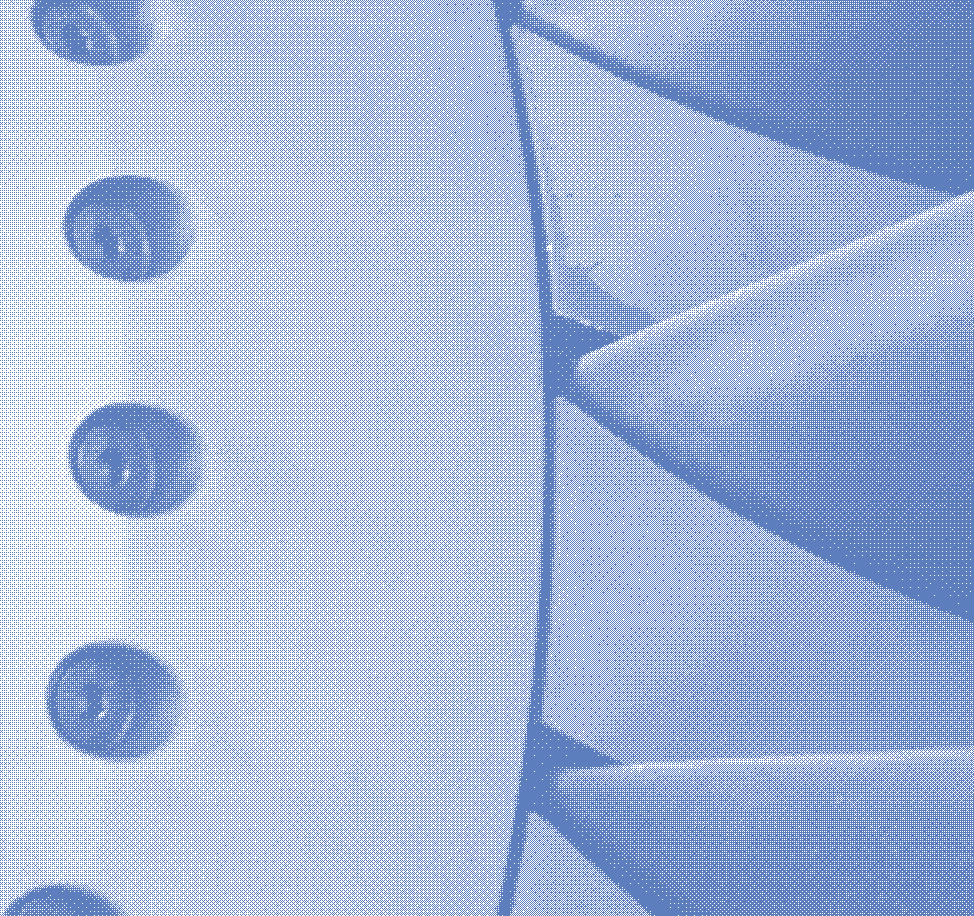
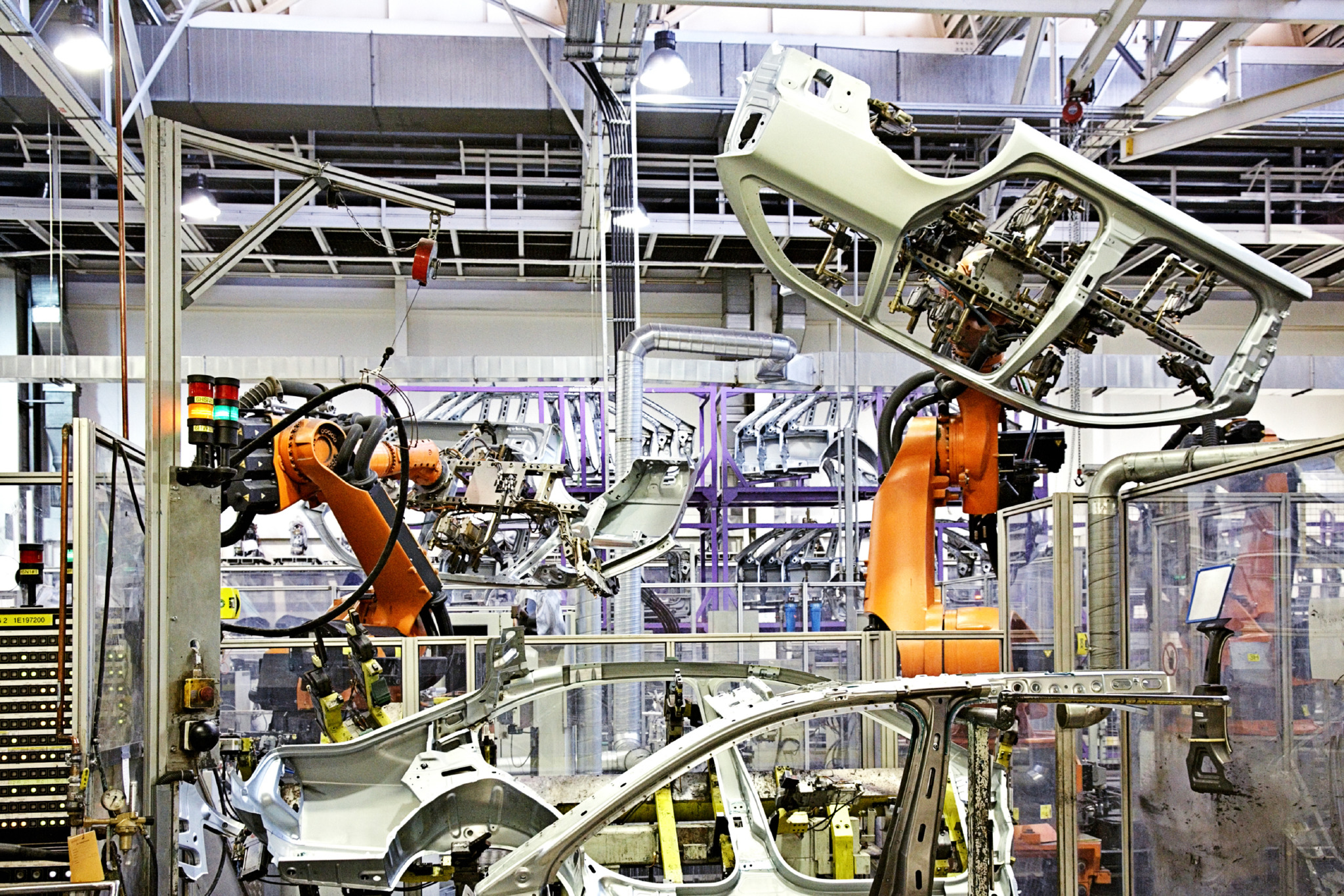
News, Views & Events
News
Mind The Gap: LightForm Bridges Microstructural Scales with New Simulation Capability
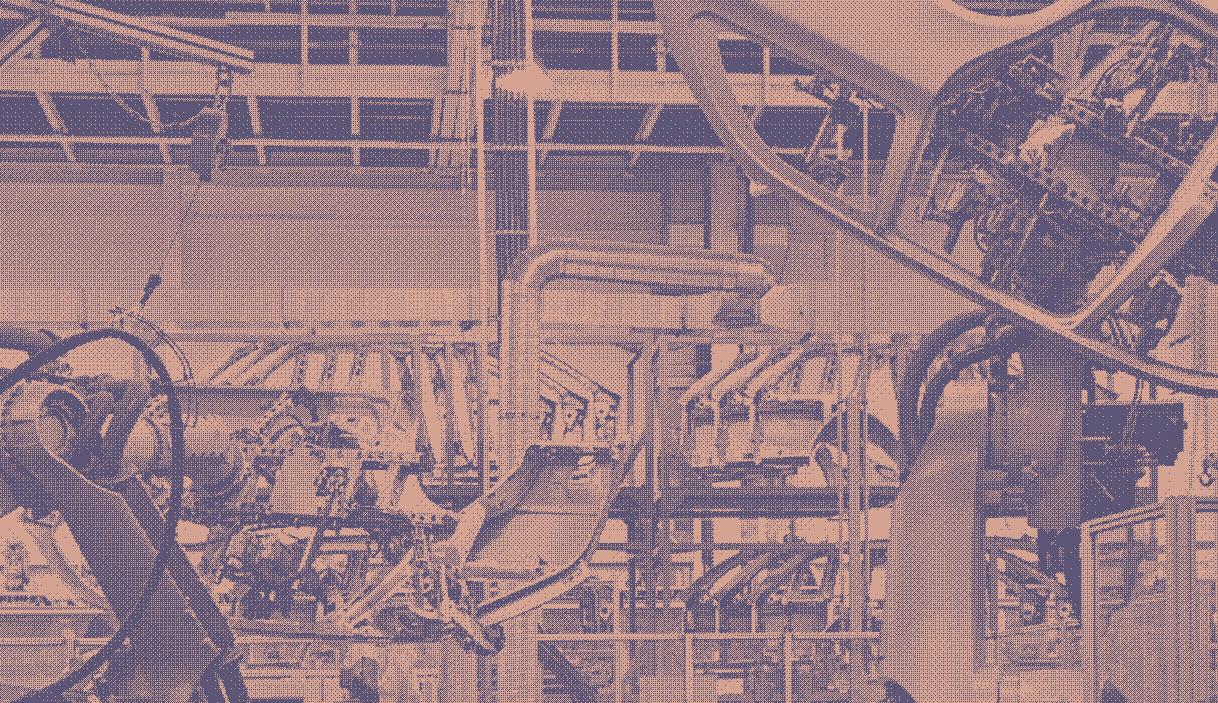
A recent breakthrough in microstructure modelling from LightForm researchers, in collaboration with the Max-Planck-Institut für Eisenforschung and Airbus, has enabled detailed predictions of microstructure evolution in high-strength aluminium alloys for the aerospace industry.
7xxx series Al-Zn-Mg-Cu alloys are widely used in aerospace components. However, their wider-scale application and further alloy development is currently being inhibited by a lack of understanding of their high susceptibility to Environmentally Assisted Cracking (EAC). EAC mitigation in these alloys is strongly linked to the microchemistry of the grain boundaries (GBs) and GB precipitates, which, being a complex function of the alloy composition and process history, is difficult to reliably predict and engineer.
Until recently, microstructure prediction models relied heavily on empirical data, making them expensive to calibrate and ill-equipped to describe complex multi-component alloys. Novel developments in simulation technology in this work has made possible, for the first time, the direct use of accurate CALPHAD multi-sublattice phase descriptions into large-scale phase-field models of microstructure evolution, thus enabling quantitative predictions of microchemistry development during commercial heat treatments in Al-Zn-Mg-Cu alloys.
This powerful simulation tool has been exploited to systematically investigate the influence of alloy composition, solute diffusivity, and heat treatment parameters on the microstructural and compositional evolution of the η-phase. Such a predictive capability will help aluminium producers accelerate alloy and process development in order to more consistently produce higher quality products, whilst reducing waste and the unnecessary use of resources throughout the industry.