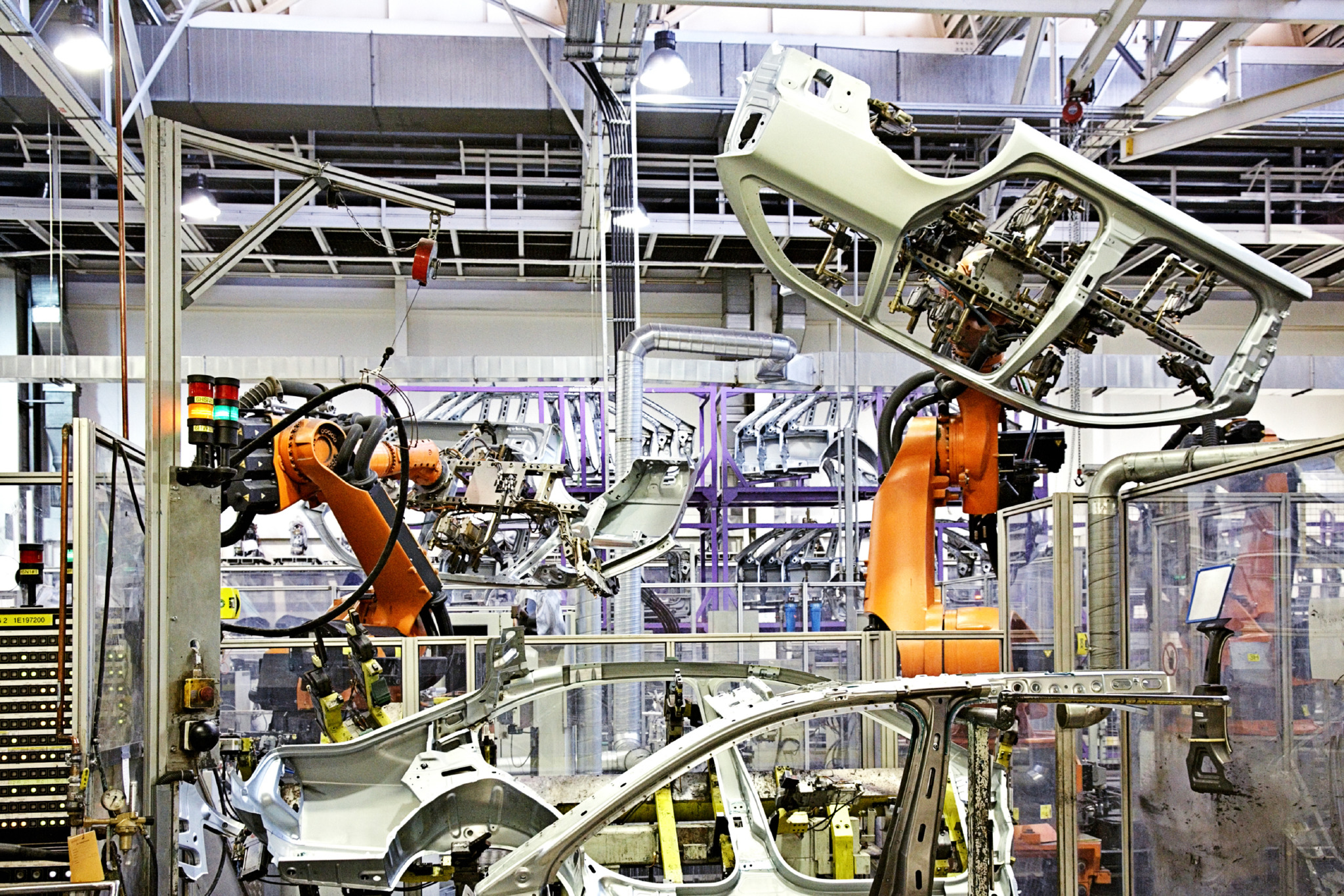
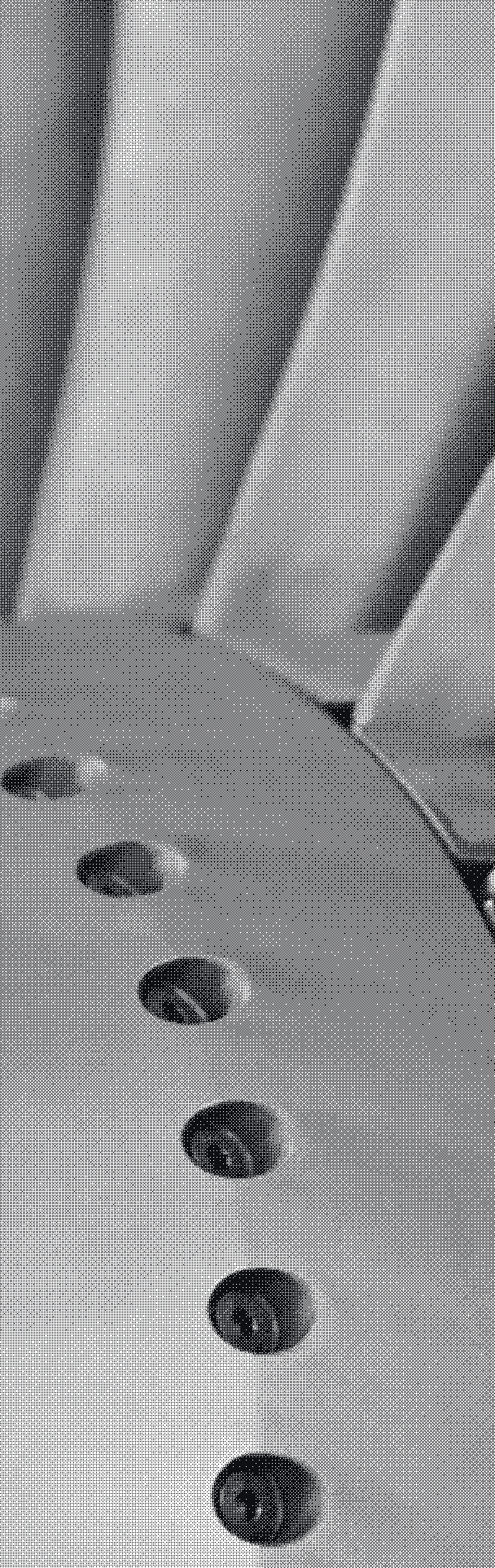
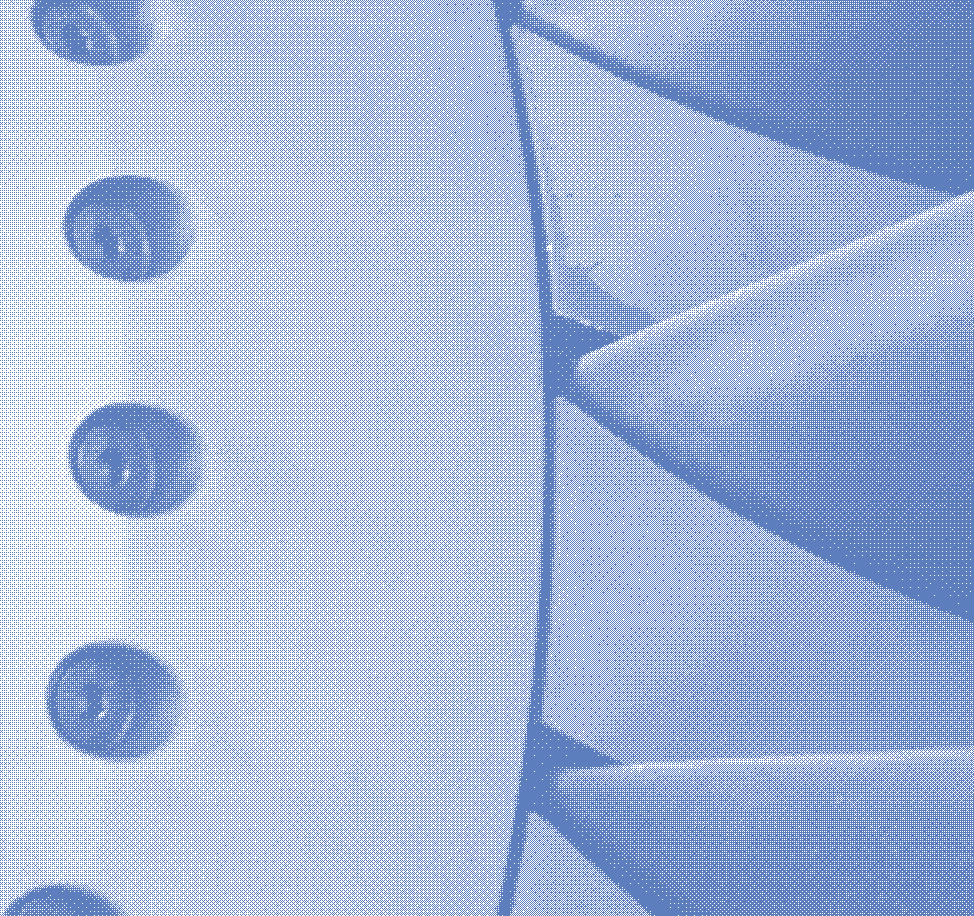
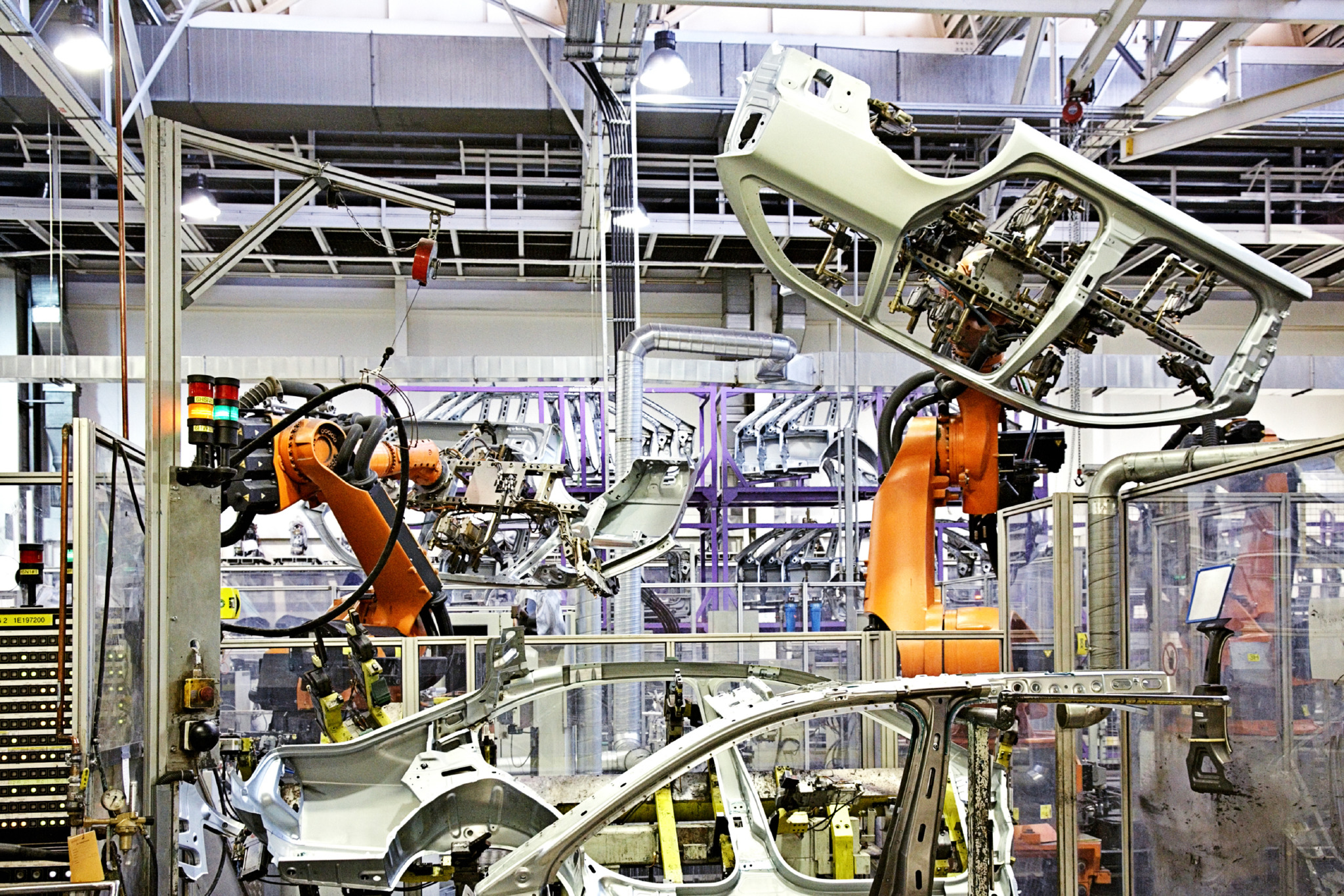
Research Projects
Aluminium
Development of compressed HFQ processing routes
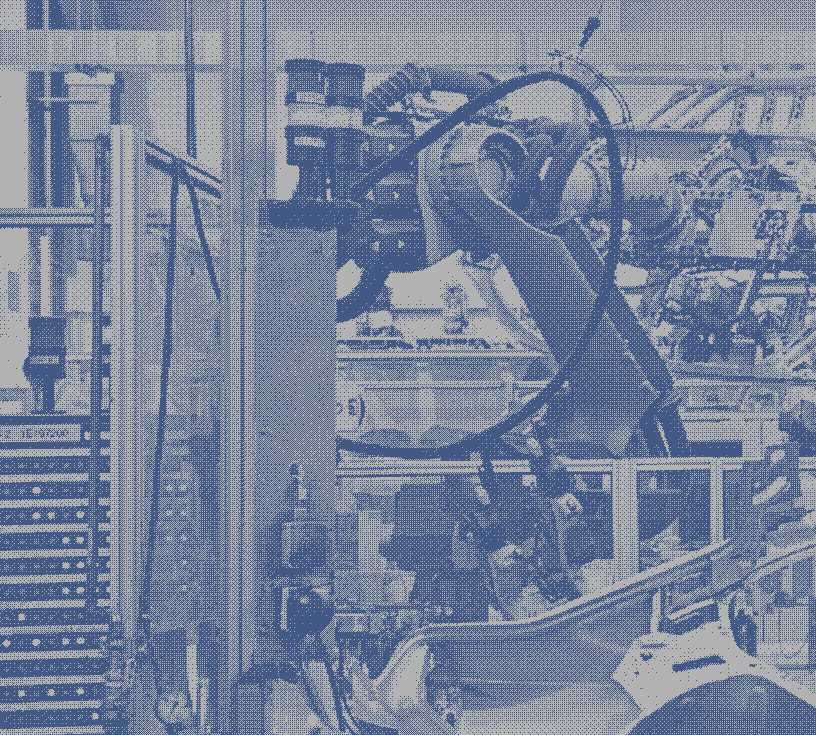
Background:
Solution heat treatment, Forming and cold die Quenching (HFQ®) is a technique that enables mass production of high strength aluminium panel parts with unprecedented shape complexity. HFQ® is being used to reduce the mass of components by using high-strength aluminium grades, such that HFQ® panels are delivering >50% weight reduction comparing to conventional steel ones, or >20% compared to some conventionally pressed aluminium grades. The key potential concerns relating to the current development are the processing cost and the lead time, which are two important factors, particularly for the car manufactures. Therefore, gaining a deeper understanding of the microstructure evolution, particularly the precipitate, during HFQ is vital to enable a more energy-efficient HFQ processing routes to be developed for the industrial application.
Aims: The project aims to establish compressed HFQ processing routes by developing rapid ageing and solution heat treatment, considering the microstructure evolutions, while maintaining or further improving the required post-form shape and mechanical properties.
Methodologies:
- Gleeble tests will be performed, simulating the HFQ procedure, to specimens to examine the optimum (cost-effective) HFQ processing parameters for solution heat treatment, quenching and ageing individually. The processing variables include heating rates, soaking time, soaking temperature, strain rates, etc.
- Mechanical tests (e.g. tensile, hardness tests, fatigue, etc.) will be conducted to examine the post-formed properties.
- Microstructure examination (e.g. SEM, EBSD, etc.) will be performed to enable insight into the HFQ mechanism.
- A typical car body component (e.g. B-pillar, etc.) will be processed using the determined parameters to validate the effectiveness of the newly established HFQ processing route.
Latest results (optimized fast ageing treatment of AA6082):
1. Fast ageing experimental examination
Tensile and TEM have been performed and given in the below figure.
The optimum pre-ageing temperature for AA6082 has been determined: 210 ˚C x 47 min. The total ageing time is reduced from 8 h (traditional T6) to 0.8 h.
2. Dislocation effects on age hardening properties
Tensile and EBSD have been performed. The results are provided below
Dislocation density (geometrically necessary ones) increased with pre-stretching levels, however, reduce the peak ageing strength.