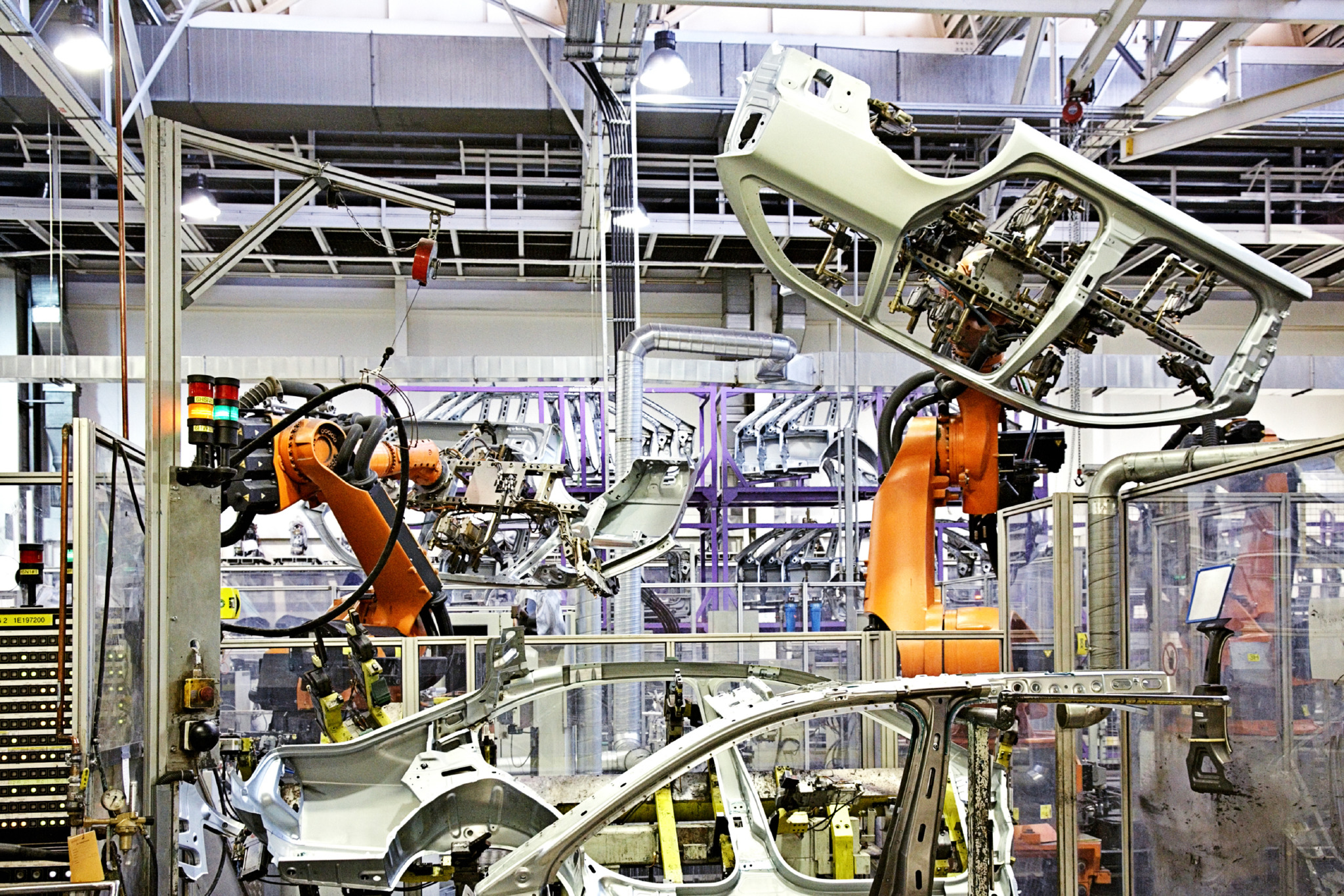
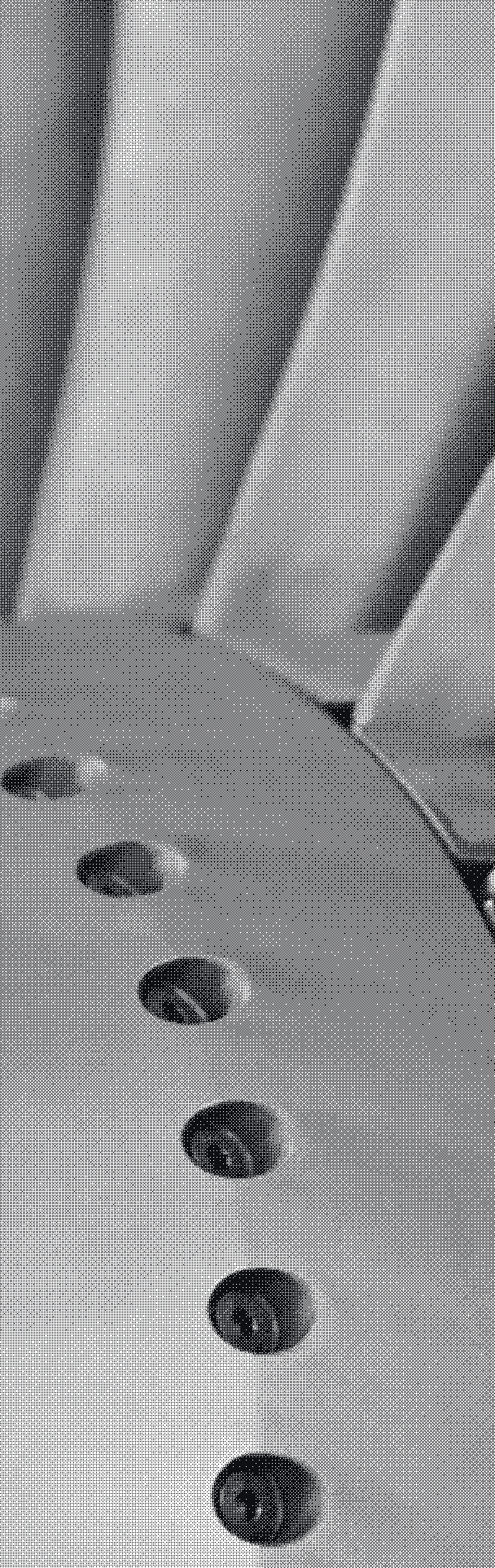
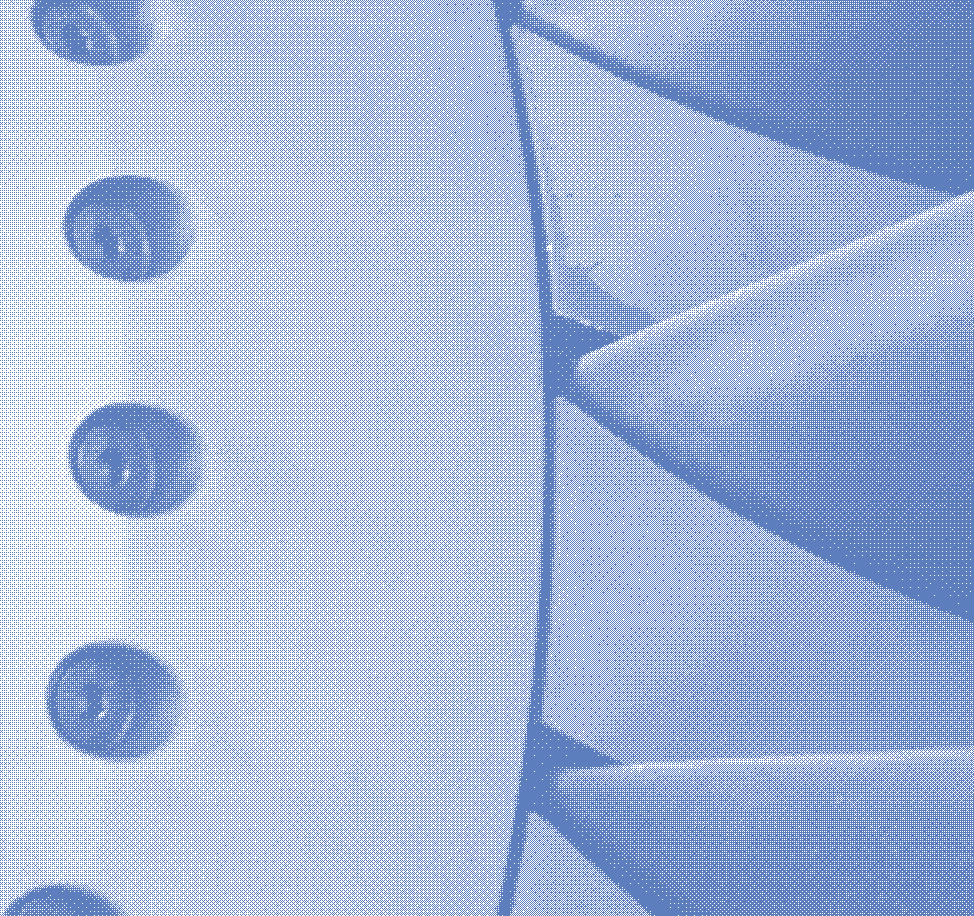
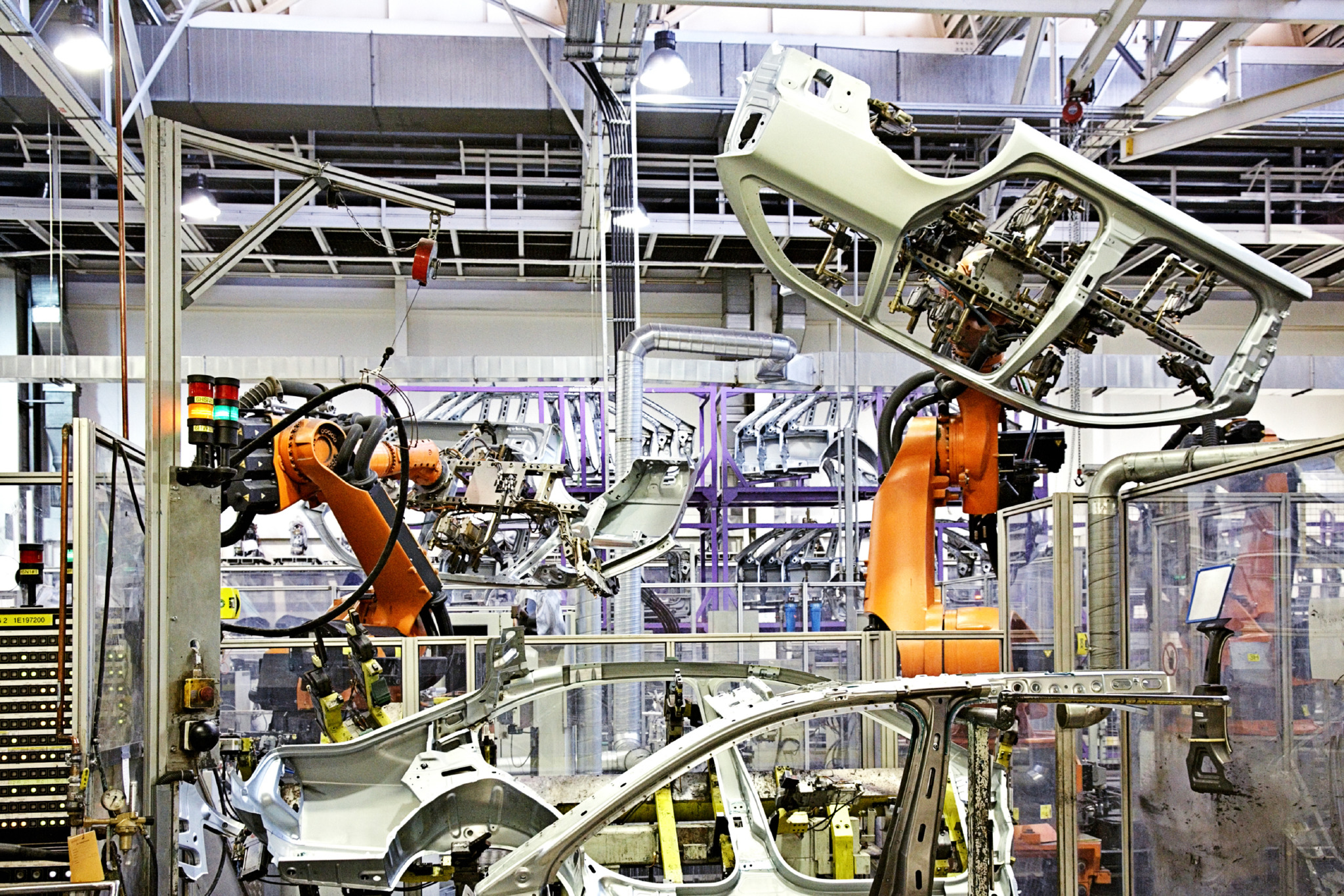
Research Projects
Titanium and Magnesium
Development of high-deposition-rate additive manufacturing processes for aerospace applications (Open Architecture Additive Manufacturing & NEWAM projects)
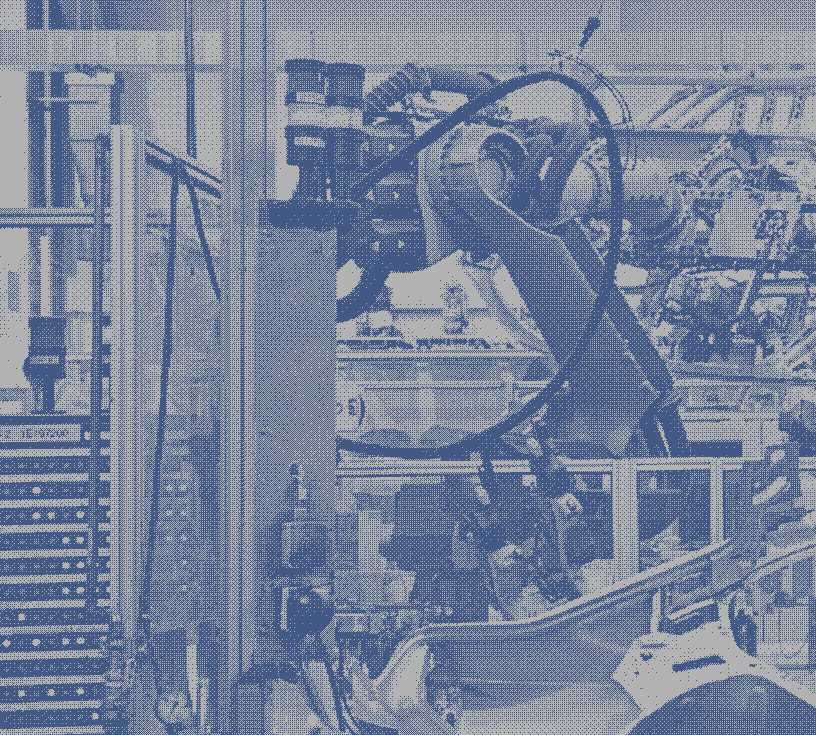
Direct energy deposition additive manufacturing processes, such as wire-arc additive manufacturing (WAAM), offer the high kg per hour deposition rates, short lead times, and large build envelopes required by aerospace, in addition to the cost and energy saving benefits. However, in particular, titanium alloy components built by these processes suffer from coarse and heterogeneous grain structures that lead to anisotropic and unreliable mechanical properties. The aim of this project is to produce refined and homogeneous grain structures in titanium AM components using process control and alloy design, and provide tailorable mechanical properties through post-build heat treatments. This has led to the development of an AM aerospace process capable of producing Ti-6Al-4V parts that can be directly substituted for current wrought counterparts in service. More recently, the research has focused on the development of ‘alloy-alloy composites’, where multi-alloy components have been deposited for tailorable, site-specific mechanical properties, which cannot be achieved by conventional casting and wrought processing routes.
This research is being conducted using high-throughput, large-area, simultaneous electron backscatter diffraction (EBSD) and energy dispersive X-ray spectroscopy mapping, 3D EBSD mapping with samples prepared using focused ion beam and laser techniques, in-situ SEM heating with concurrent EBSD mapping, electron probe microanalysis chemical mapping, transmission electron microscopy, and crystal plasticity finite element modelling using the DAMASK and MatFlow packages.