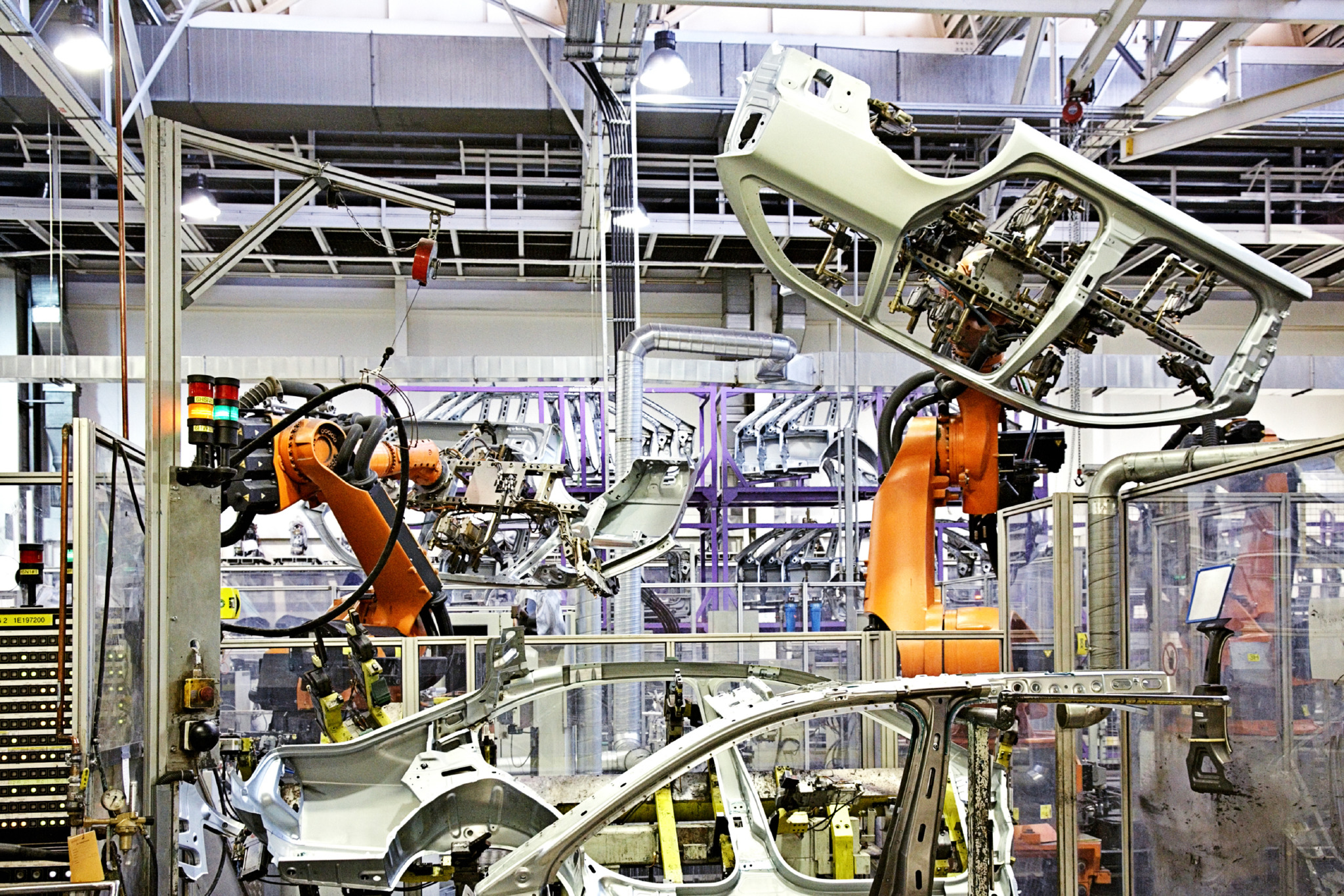
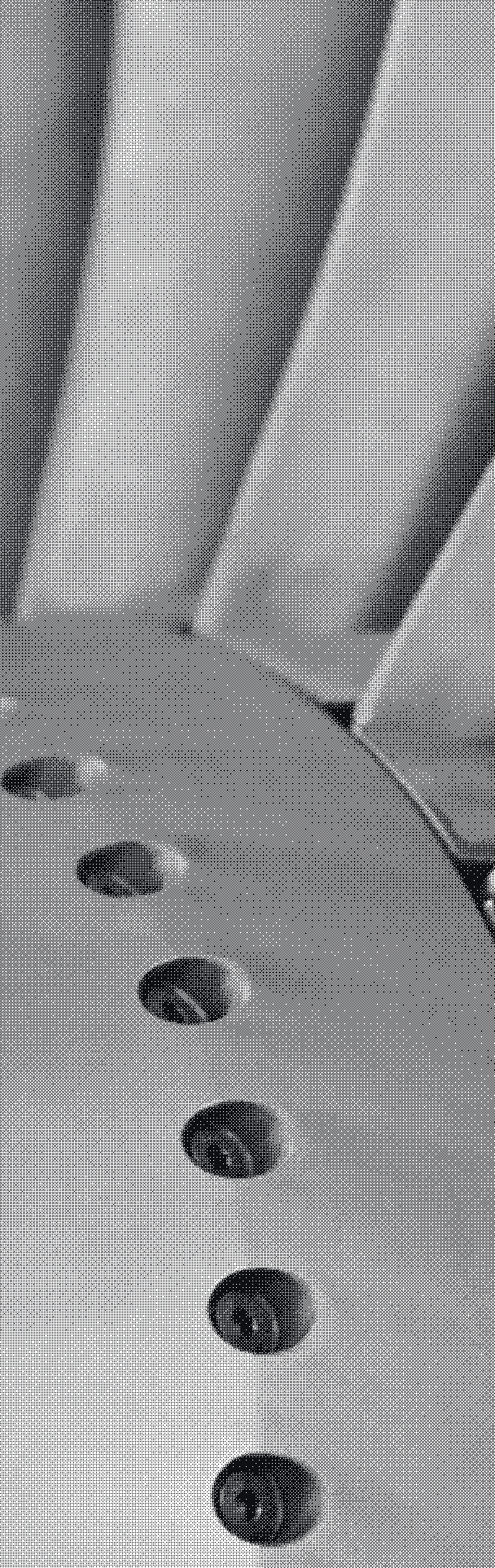
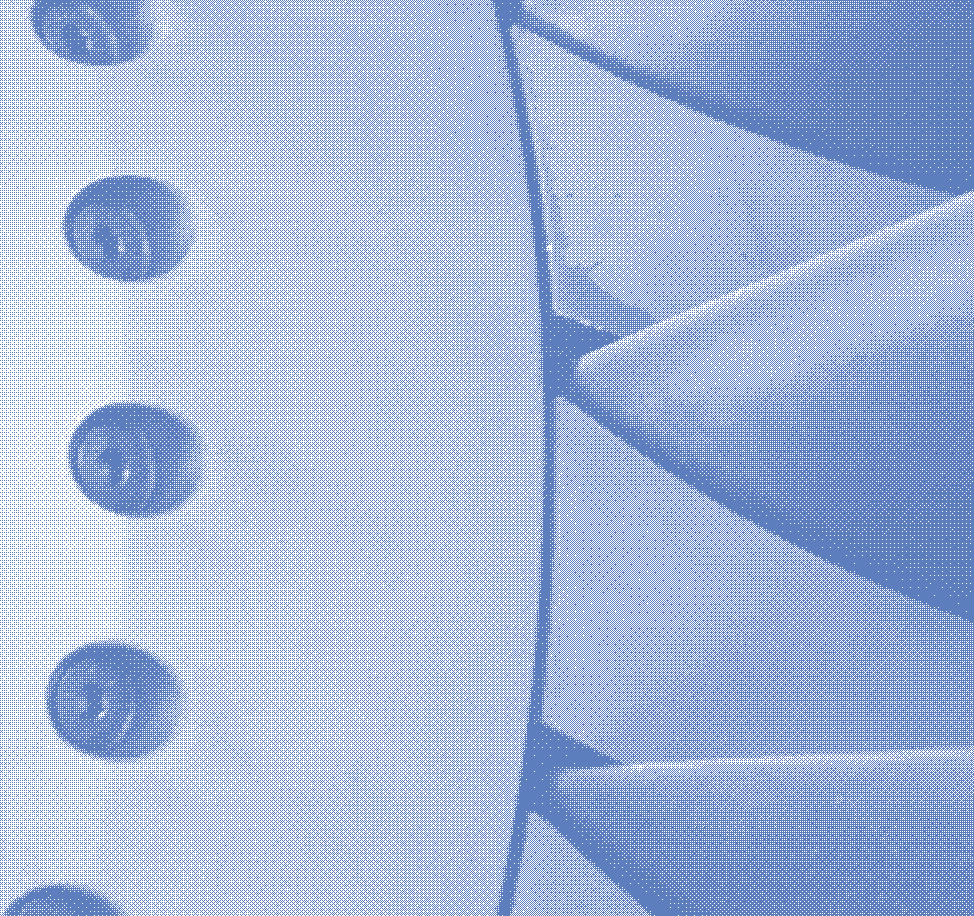
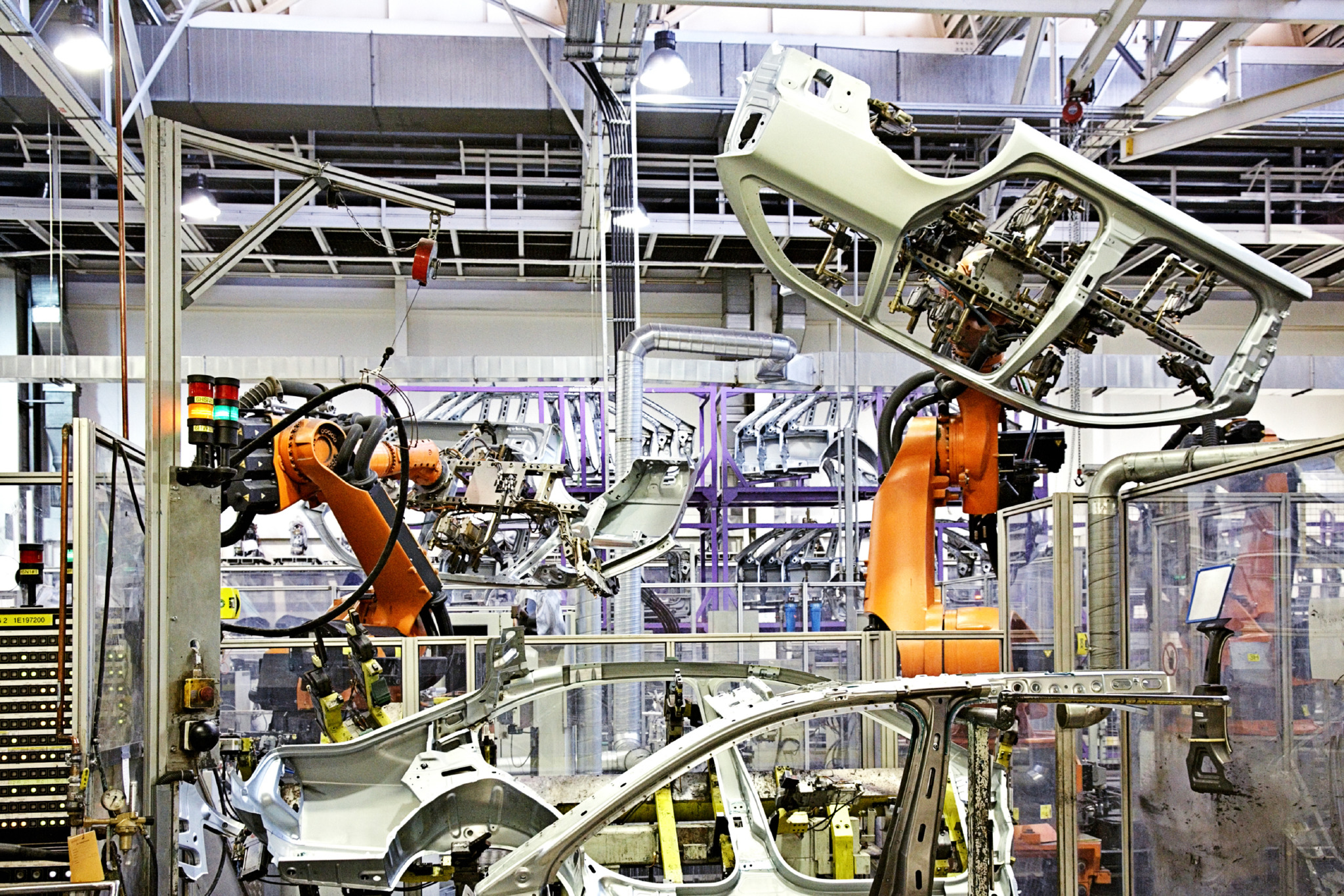
Research Projects
Titanium and Magnesium
Development of novel hot stamping process of titanium alloy
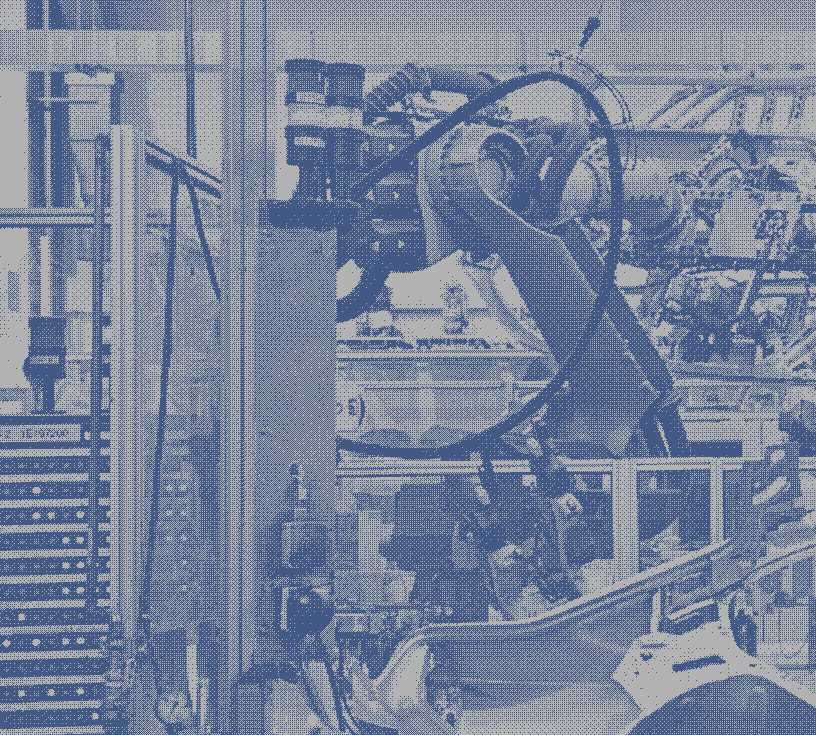
To meet the demand for lower global emission and fuel consumption, the application of titanium alloys with high strength and low density have expanded greatly in the field of aerospace. The currently used manufacturing methods in aerospace industry consist of Superplastic Forming (SPF) and Isothermal Stamping (IS), which are time, energy and cost intensive. The traditional hot stamping and cold die quenching method is first proposed for steel and then aluminium alloy panel forming. However, limited researches focus on hot stamping of titanium alloys. To overcome the drawbacks of SPF and IS, increase production efficiency and reduce manufacturing costs, a new hybrid forming method combining heat treatment and fast stamping named Heat Stamping (HS) is proposed and to be developed in this project for titanium alloys. To investigate the heat stamping process of titanium alloy Ti-6Al-4V, metallurgical and thermo-mechanical responses and their interactions under HS conditions need to be determined.
The aim of the project is to develop a novel, cost-effective Heat Stamping (HS) process for forming complex-shaped titanium alloy panel components with low energy consumption. The new process will allow significantly reduced cycle time and low temperature dies to be used for cost reduction.
Methodologies:
- Understand the metallurgical and thermos-mechanical responses, and their interactions, of two-phase Ti-6Al-4V.
- Develop mechanism-based unified viscoplastic constitutive model and phase transformation model for two-phase Ti-6Al-4V under Heat Stamping conditions.
- Establish processing modelling system for simulations and optimisations through calibrating the material models using heat stamping experimental data and implementing the models in finite element software.
- Design and manufacture laboratory scale heat stamping rigs with support of Doncasters (industrial sponsor) and produce demonstrator model component.
Latest results (Strain rate sensitivity tests)
- High strain rate tensile tests conducted at higher forming temperatures were found to have higher strain rate sensitivity;
- Although the strain rate sensitivity of specimen in uniaxial tensile tests with step quenching (950-800 ) prior to deformation is lower than direct test at high temperatures (950-800 ), it is still higher than that of specimen tested at 800 .