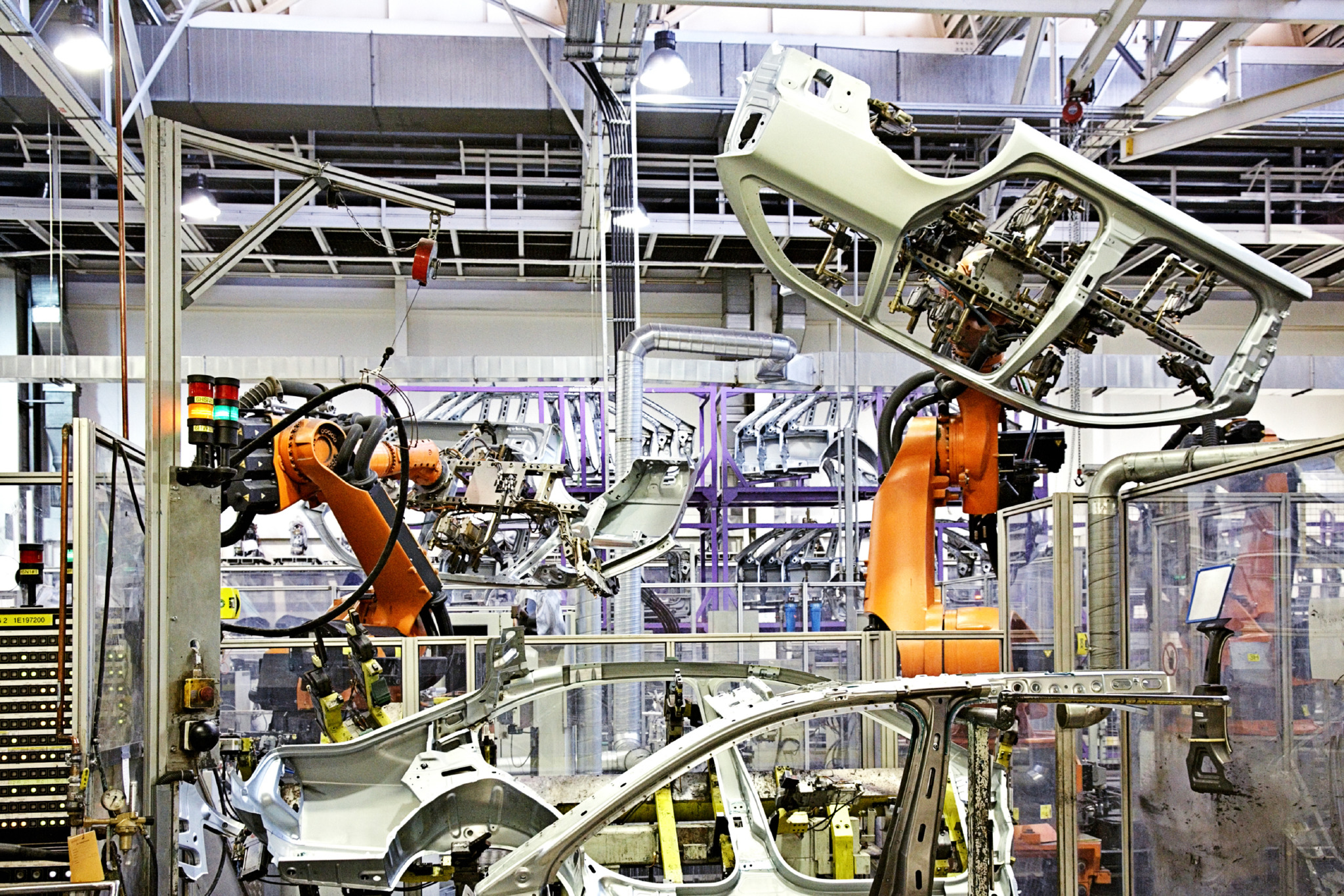
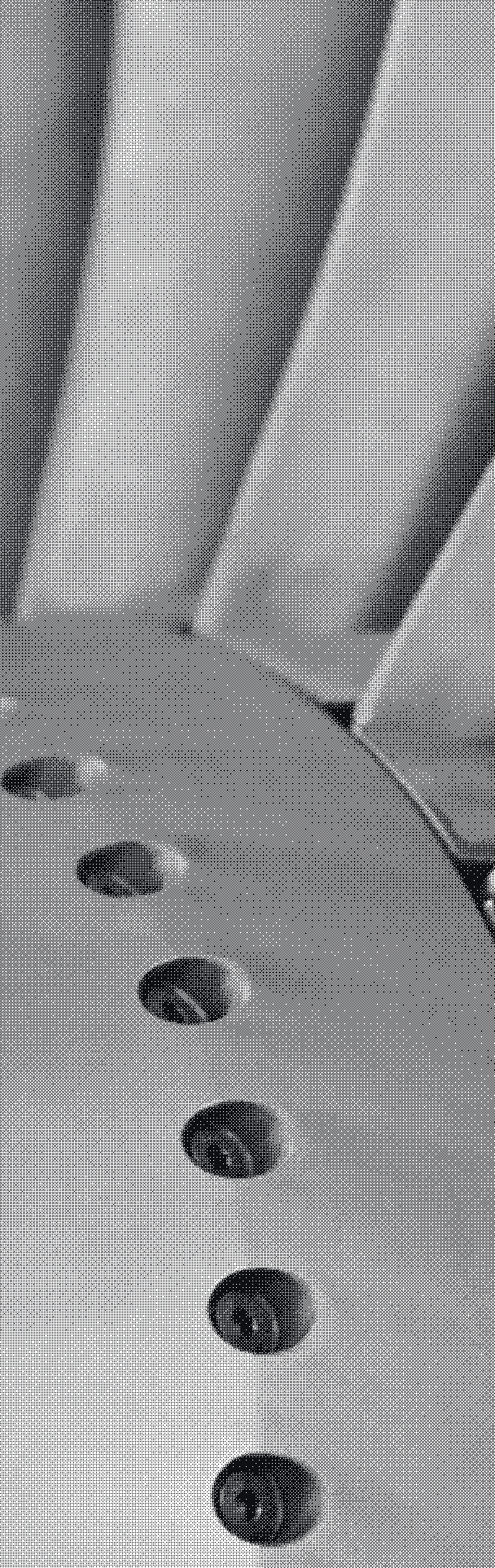
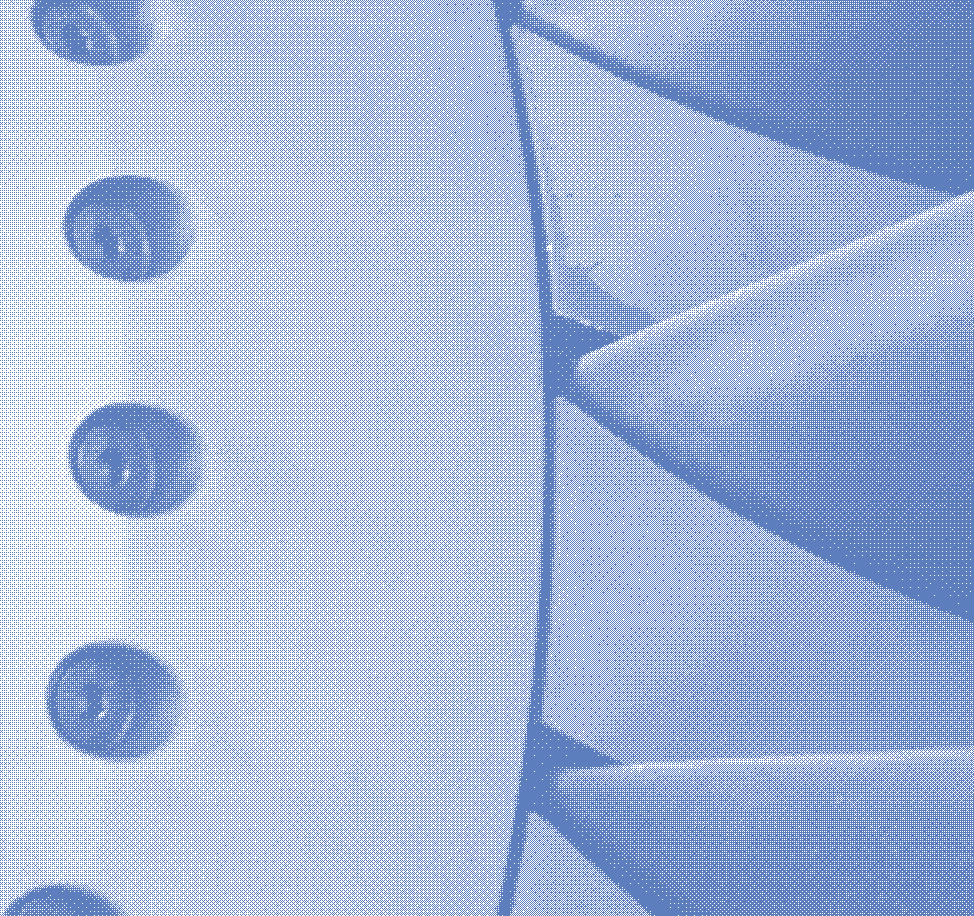
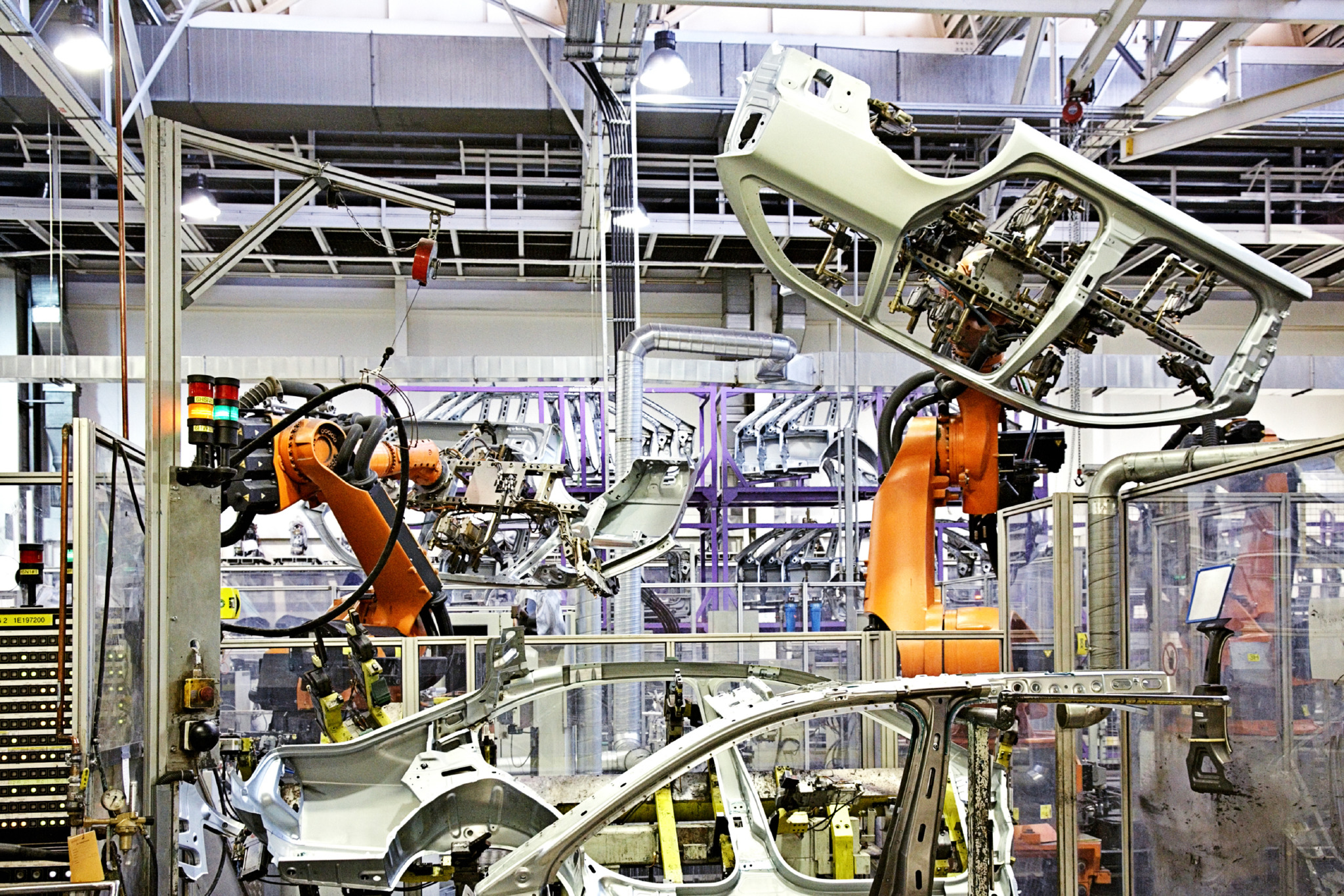
Research Projects
Aluminium
Improving the Hot Form Quench (HFQ) process in 6XXX aluminium alloys - Dr Paloma Hidalgo-Manrique
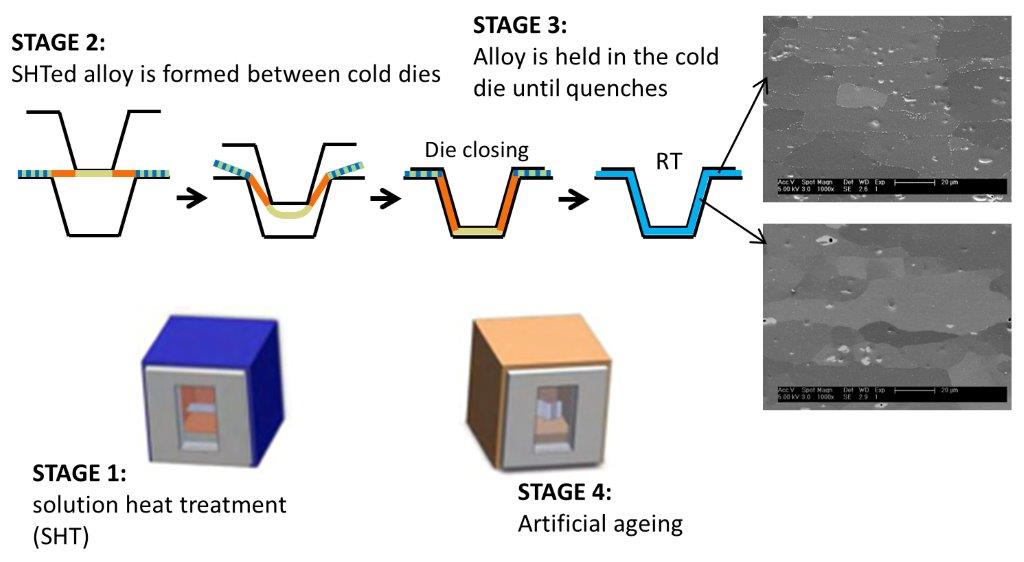
Hot Form Quench (HFQ) is a process in which stamping and heat treating are combined in a single operation to produce complex-shaped Al components from high-strength Al alloys. In the HFQ process, an Al sheet is solution heat treated, then pressed to shape while still hot. The part is quenched in the die, followed by ageing to the T6 condition. This process allows for a greater draw depth, which significantly reduces assembly operations, tooling design and design operations as well as improves the strength of the material. As a result, thinner material can be used to gain significant weight and cost savings and reduce CO2 emissions by the transport industry. However, the optimisation of the different steps involved in the HFQ process is crucial to obtain high-performance components while increasing at sustainable costs.
This project is aimed at studying the effect of different post-forming ageing treatments on the microstructure and thus mechanical properties and corrosion resistance of HFQ parts. For this purpose, commercially produced HFQ automotive parts have been supplied by the company Impression Technologies Ltd. The microstructure and performance of different regions of these parts are being examined to understand the interaction between the forming process variables (temperature and local strain history), microstructure and performance. For the microstructural characterisation, a combination of complementary techniques, including scanning and transmission electron microscopy is being used.