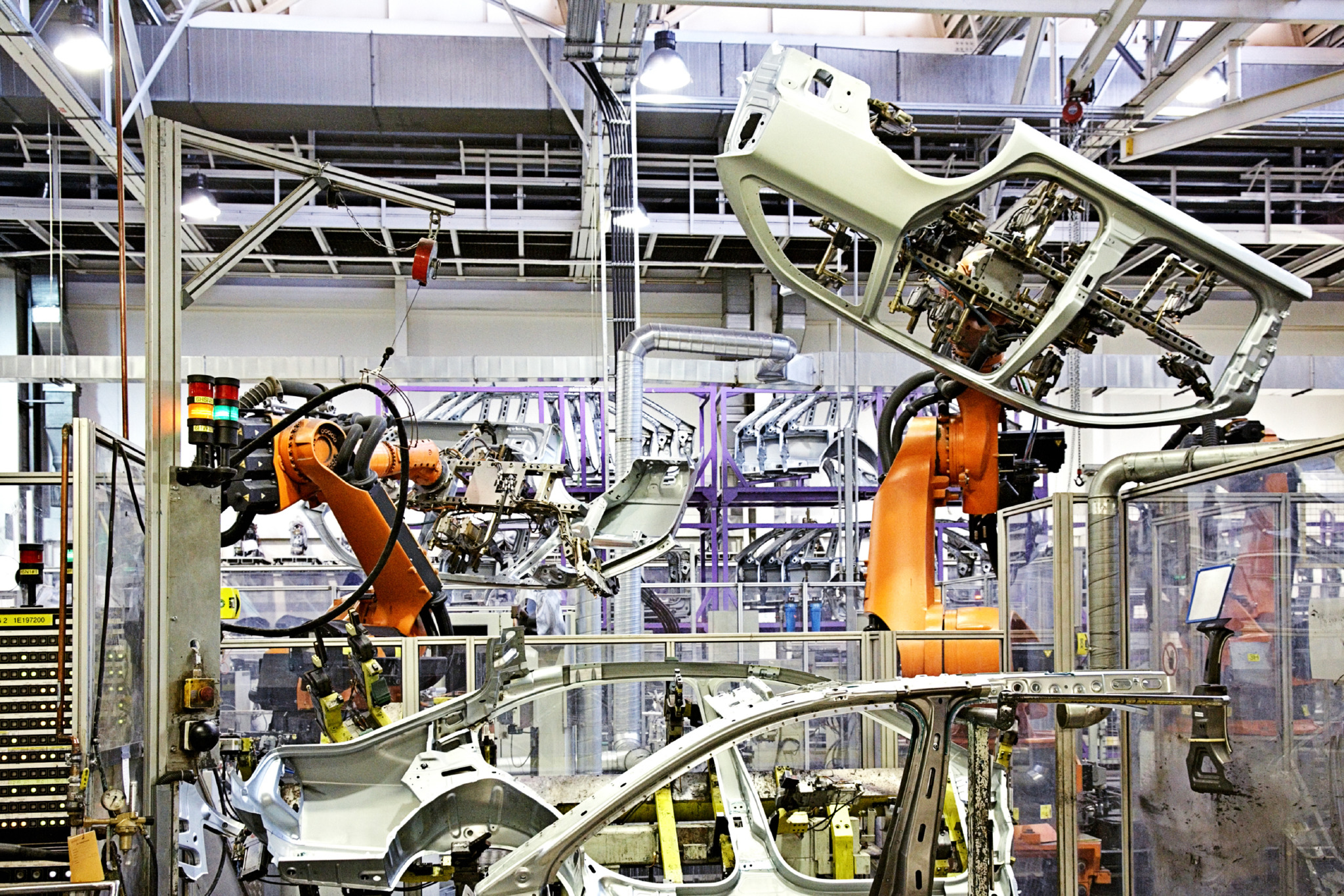
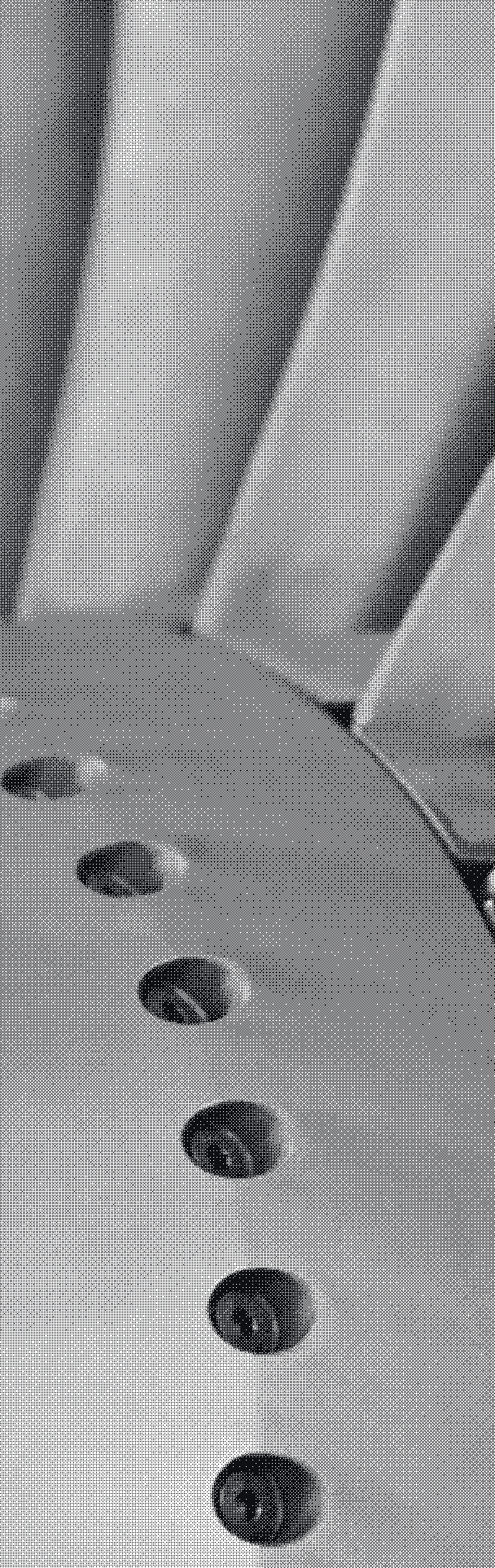
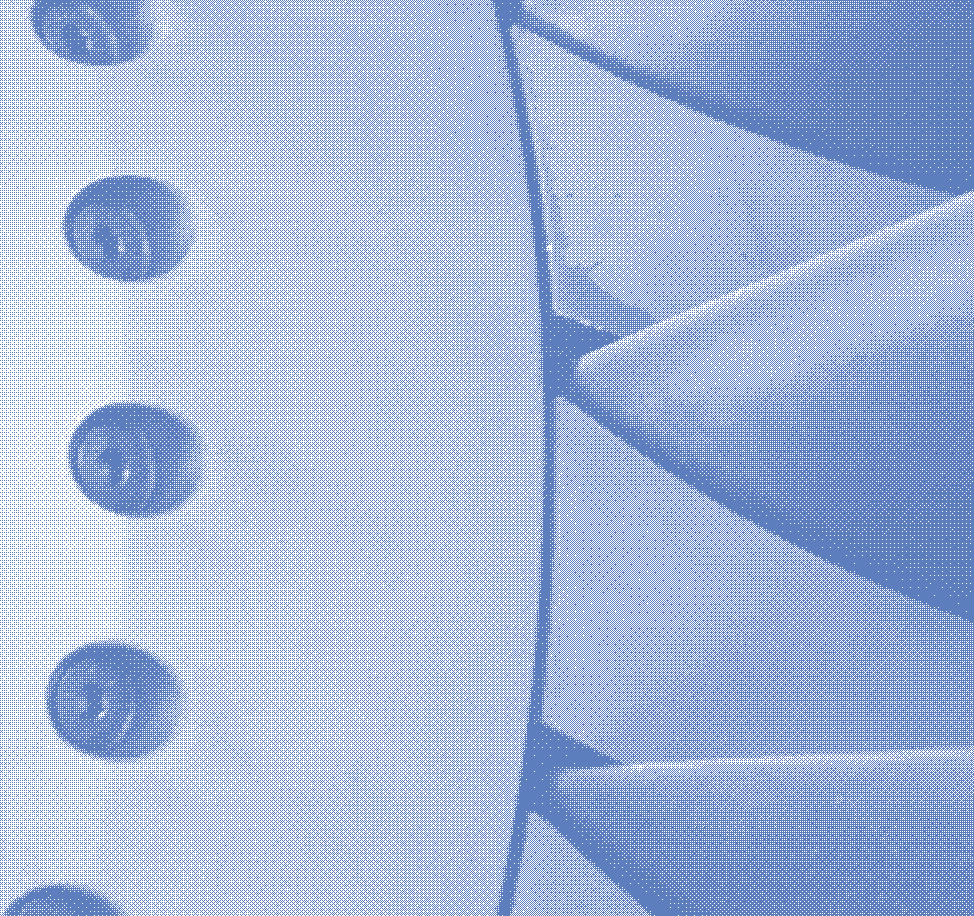
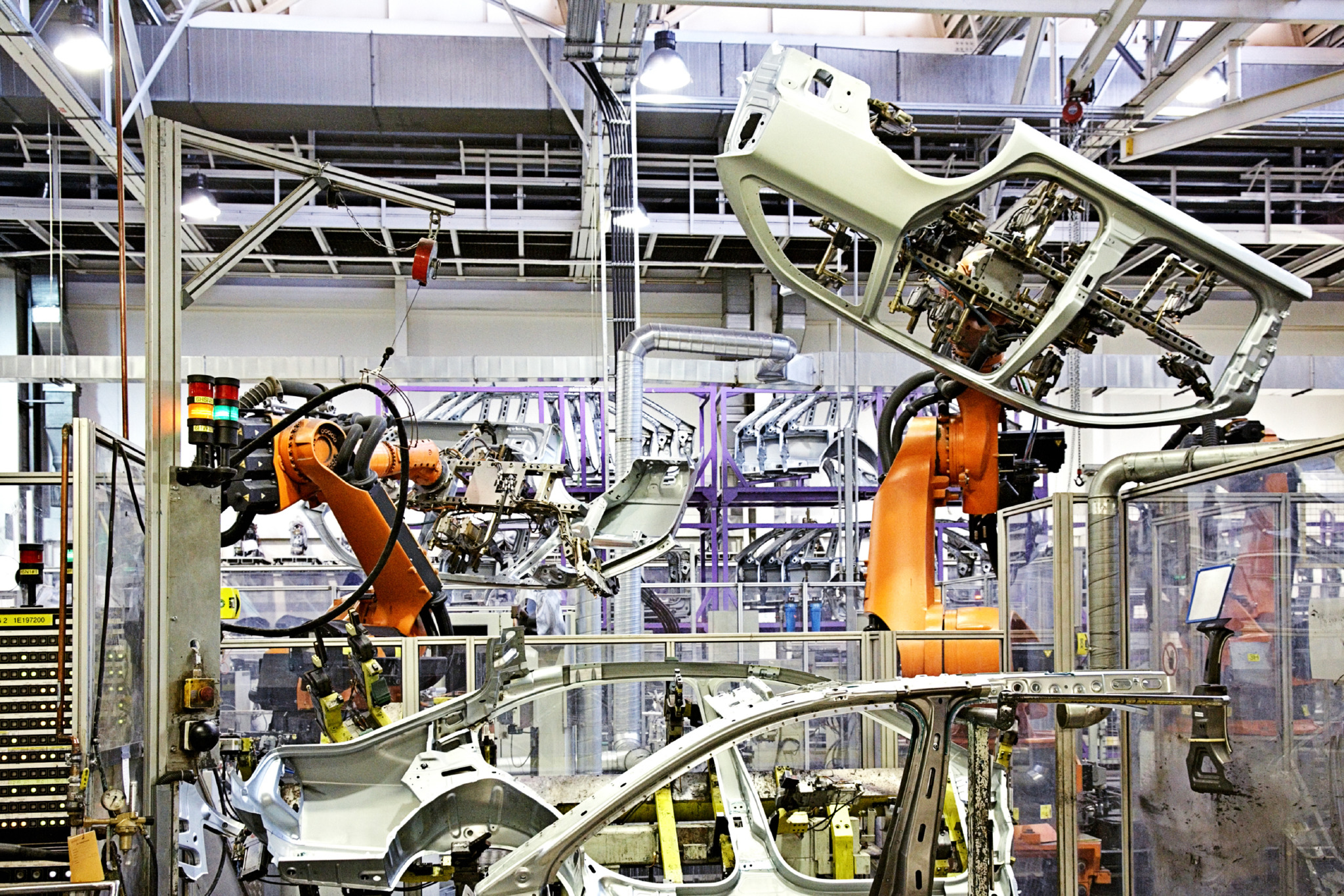
Research Projects
Titanium and Magnesium
In-situ characterisation of the high temperature deformation micromechanics in dual-phase Ti alloys
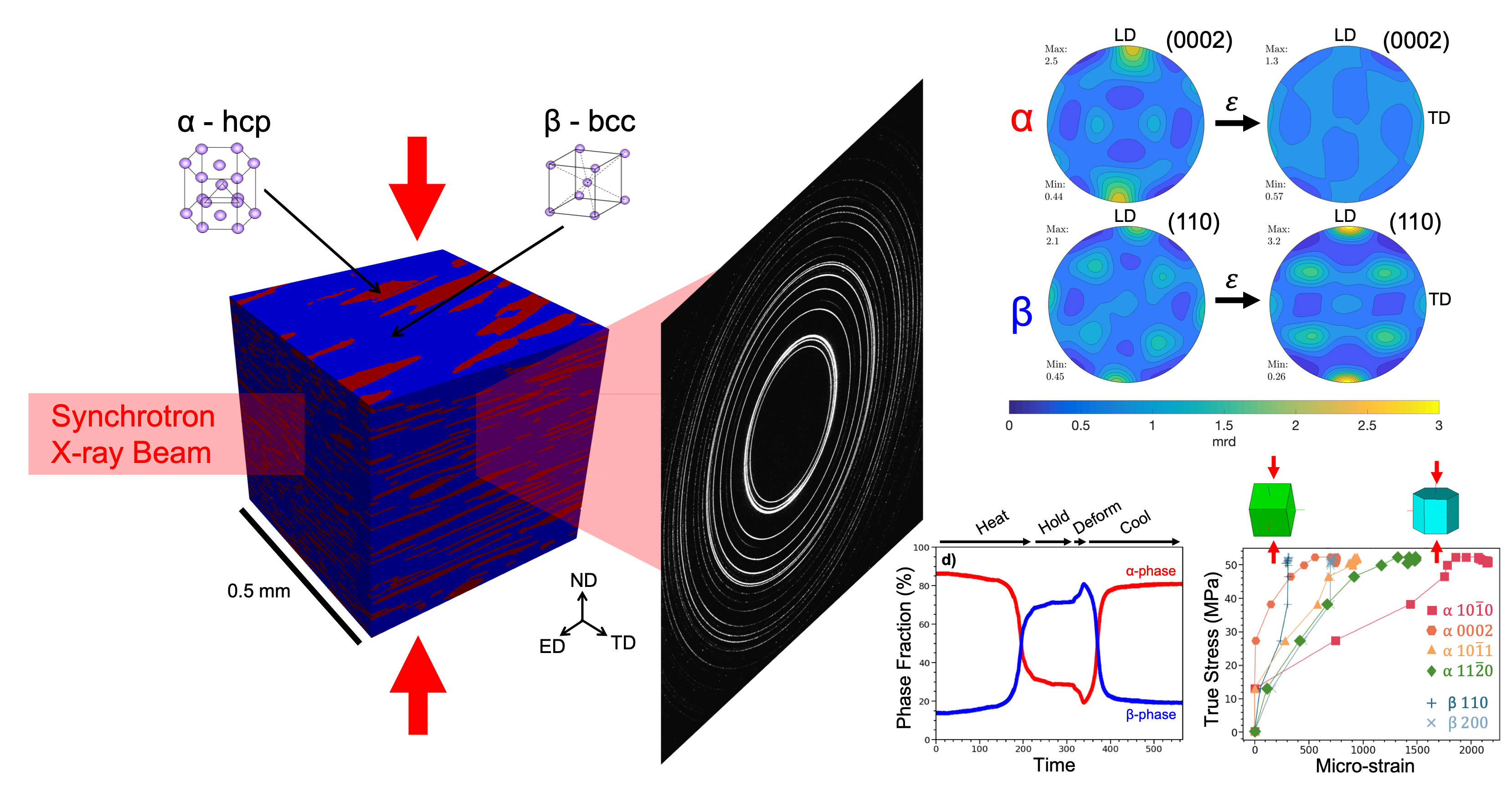
Microstructure and crystallographic orientation (texture) in dual-phase Ti-6Al-4V materials is controlled by thermomechanical processing during manufacture, offering a unique combination of properties to tailor the performance requirements of aerospace components. Nevertheless, material evolution is difficult to predict in dual-phase alloys, due to complex multi-scale interactions between the α (hexagonal-close-packed, hcp) and β (body-centred-cubic, bcc) phases, occurring during both deformation and phase transformation. In this project, we aim to improve our understanding and the predictions of processing simulations by studying the deformation of these alloys in-situ, observing microstructure evolution throughout entire thermomechanical cycles.
We are currently developing in-situ experiments using synchrotron X-ray diffraction (SXRD), using new simulation rigs, to provide time-resolved data that will be used to measure the dynamic interactions and micromechanical properties of the two phases. To date, SXRD experiments have been conducted at the Diamond Light Source’s I12:JEEP beamline and DESY’s P07(HEMS) beamline, using novel setups with an electro thermal mechanical tester (ETMT) and a deformation dilatometer, able to deform Ti-6Al-4V samples in either uniaxial tension and compression, at high temperature (850ºC – 1000ºC), whilst continuously monitoring diffraction ring patterns on a fast acquisition 2D detector.
The determination of internal elastic lattice strain evolution, dynamic phase transformation and grain reorientation, is being supported through the development of new data analysis scripts in the Python computing environment. This includes xrdfit, a new Python package for automating single peak profile fitting, and an MTEX/MATLAB extension for a Fourier-based intensity fitting method that can automate texture calculation, able to provide accurate and reproducible measurements through the batch-processing of many thousands of diffraction pattern ring images. These SXRD results will now be combined with FE models of the tests, to correlate the evolution of micromechanical properties and texture changes with the exact deformation conditions experienced at the centre of the samples.
The long-term goal in LightForm is to use these in-situ results to establish physically-based predictive microstructure evolution models, to enable optimisation of the fabrication route and support tailoring the properties of two-phase Ti alloys to meet the demands of the aerospace industries.