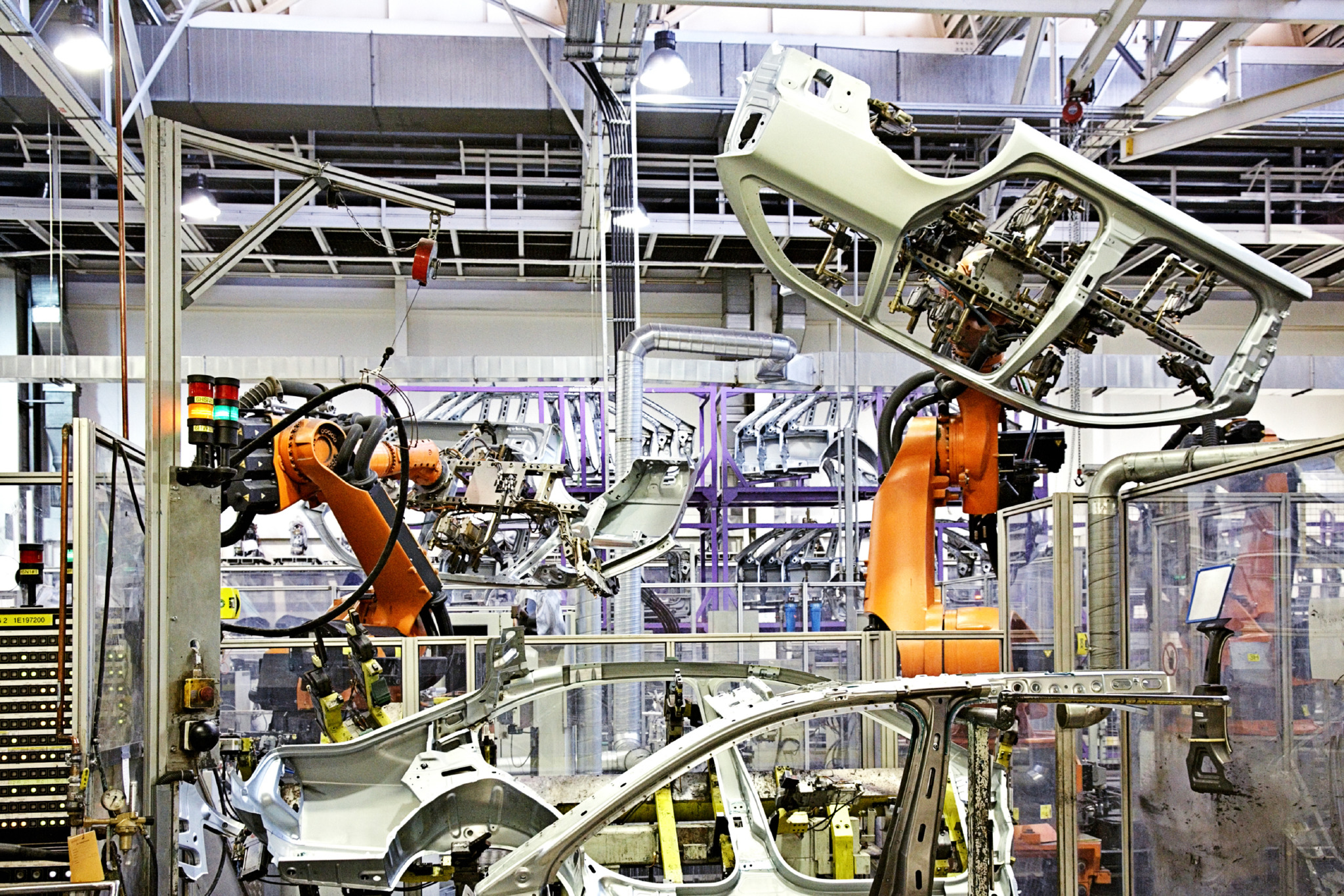
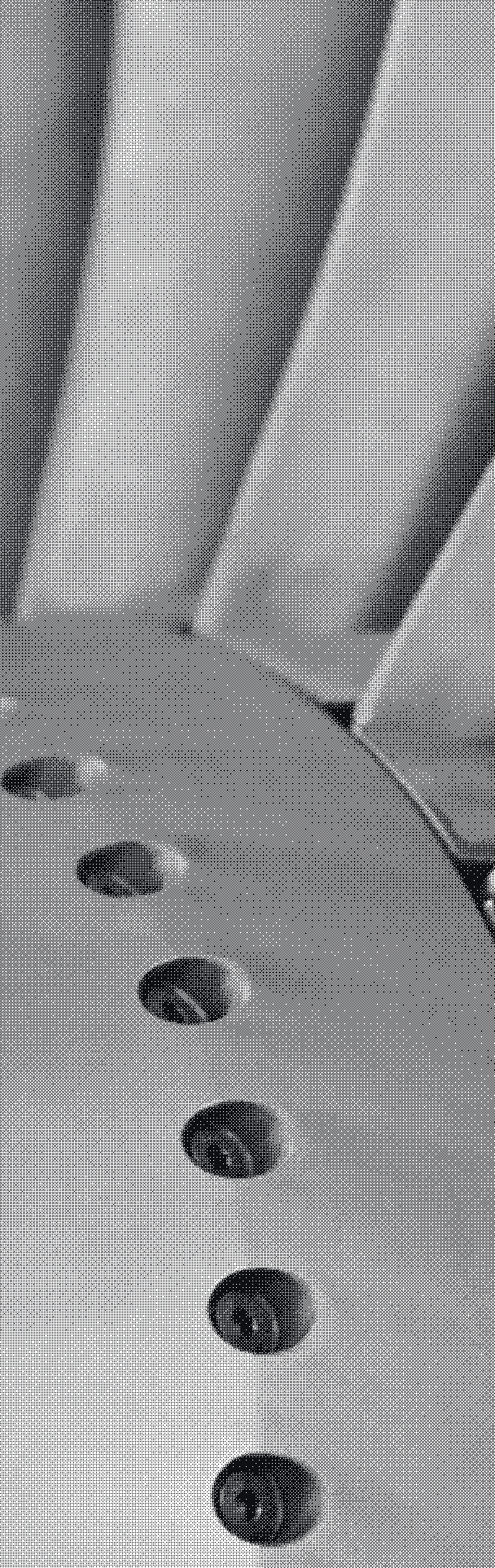
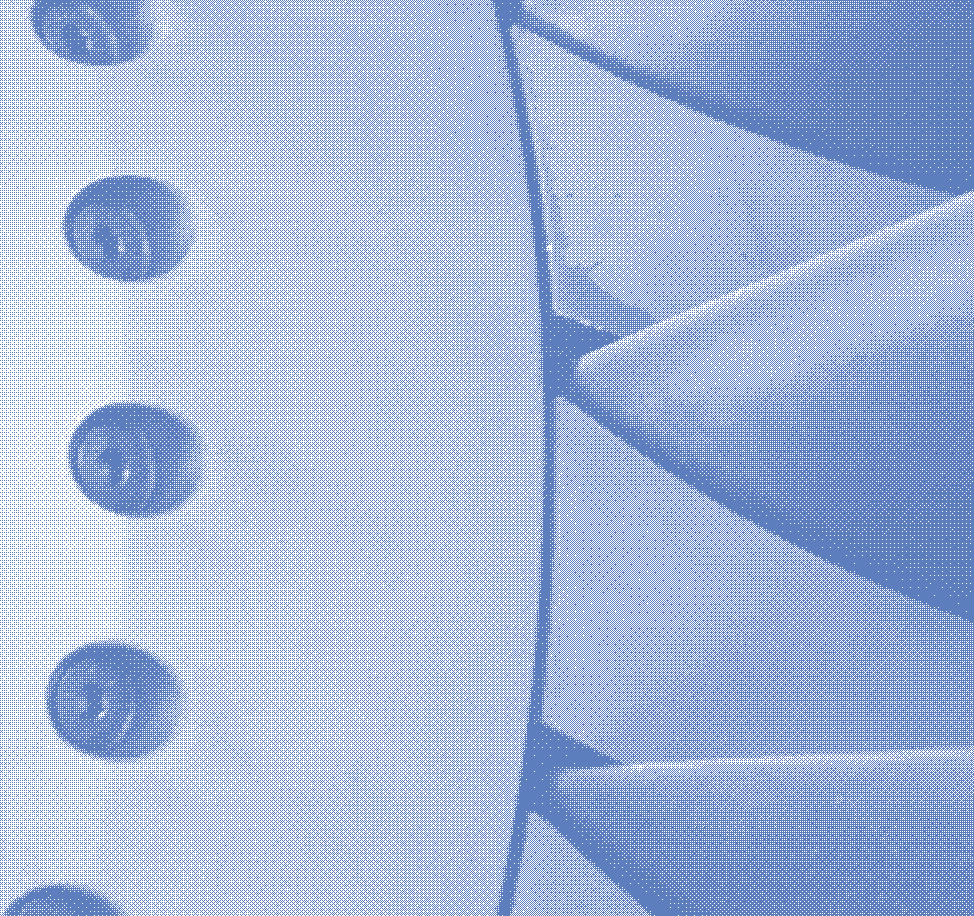
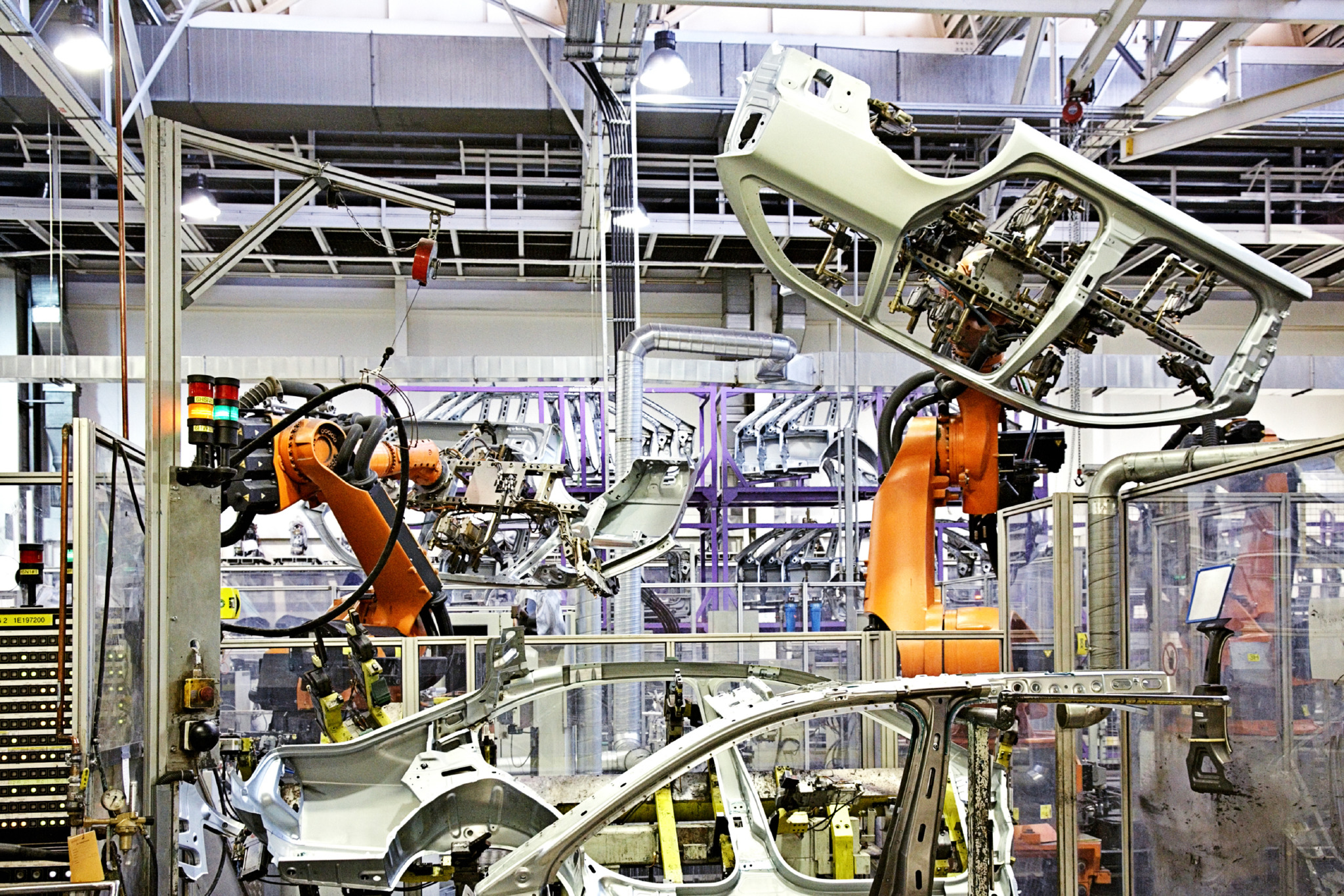
Research Projects
Titanium and Magnesium
The effects of microstructure on the ductility of aerospace titanium alloys
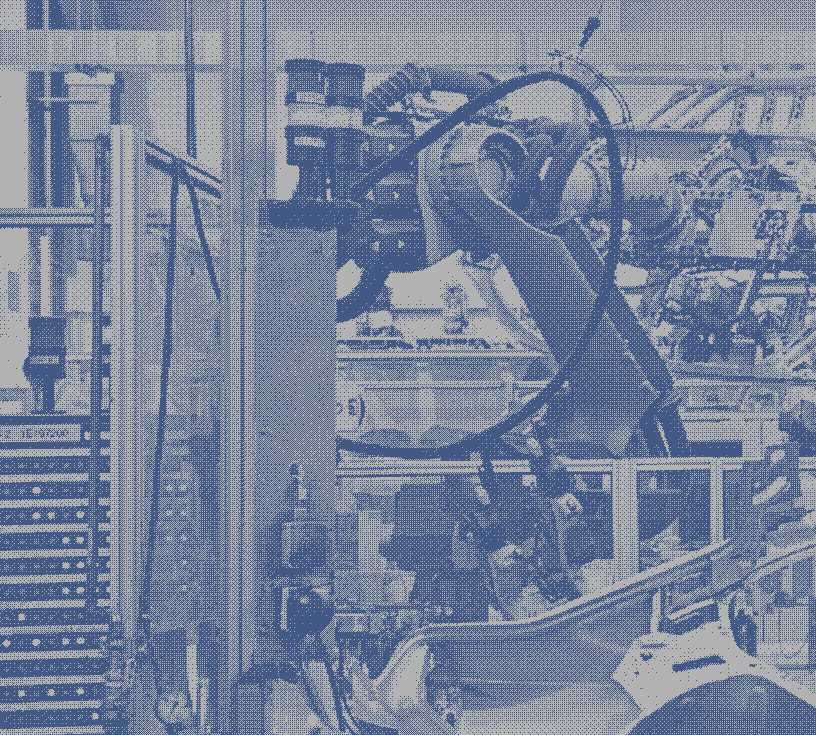
Titanium alloys are used in a wide variety of components throughout the fan and compressor stages of an aero-engine. Although engine design has evolved significantly in recent years to reduce life-cycle cost, reduce weight and improve efficiency, engine makers have continued to use the same, well-known alloys for which there are decades of experience and well established manufacturing routes. However, the limitations of these alloys are now hindering new designs, stimulating the development of new alloys with different microstructures and different property balances. The aim of the research is to understand the effects of the microstructure on the ductility of these new alloys and how they compare with the more standard alloys and microstructures currently used.
The project will combine advanced ductility testing, using in-situ deformation mapping at the macro and microscale with advanced characterisation techniques, including high resolution scanning electron microscopy, synchrotron X-ray diffraction and 3D tomography. Computational models of microstructural deformation will also be applied to understand and interpret the experimental results.
The aim of the project is to better understand the link between microstructure and texture, and ductility in alpha+ beta Ti alloys. To achieve this, the following objectives have been set:
- Measure ductility in uniaxial tension and correlate with microstructure.
- Characterise damage evolution during failure
- Investigate effects of strain path: biaxial vs. uniaxial testing
Results from tensile testing using DIC show that loading direction plays a part in in behaviour. Rolling direction and transverse direction are strongest in Ti64 and Ti407 respectively. For both alloys, 45 has longest strain to fracture.
This behaviour is due to the texture of the starting material as shown on the pole figures below.