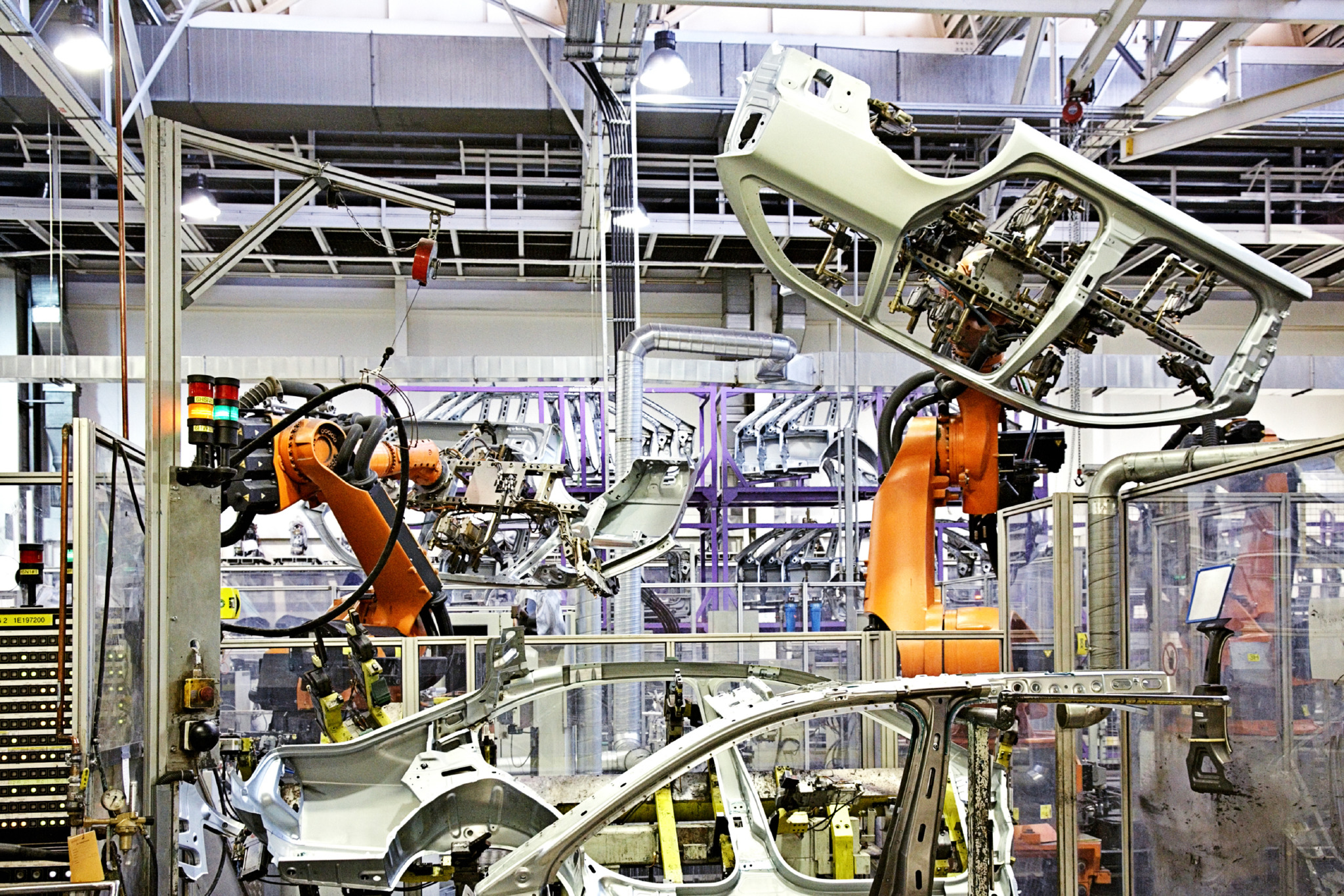
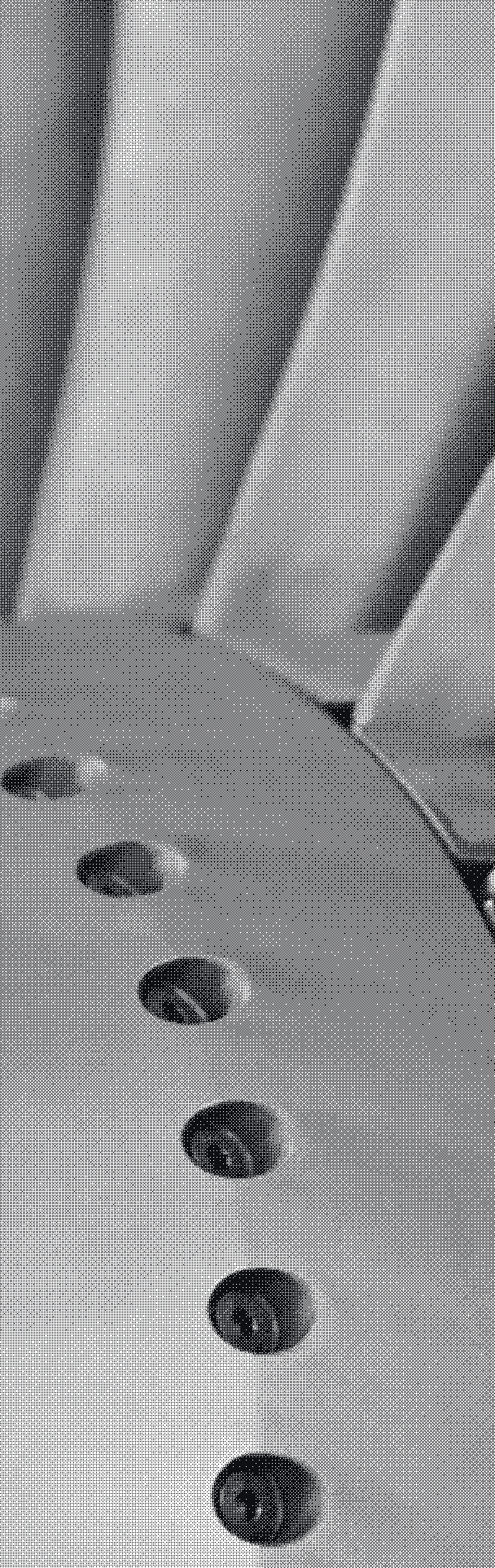
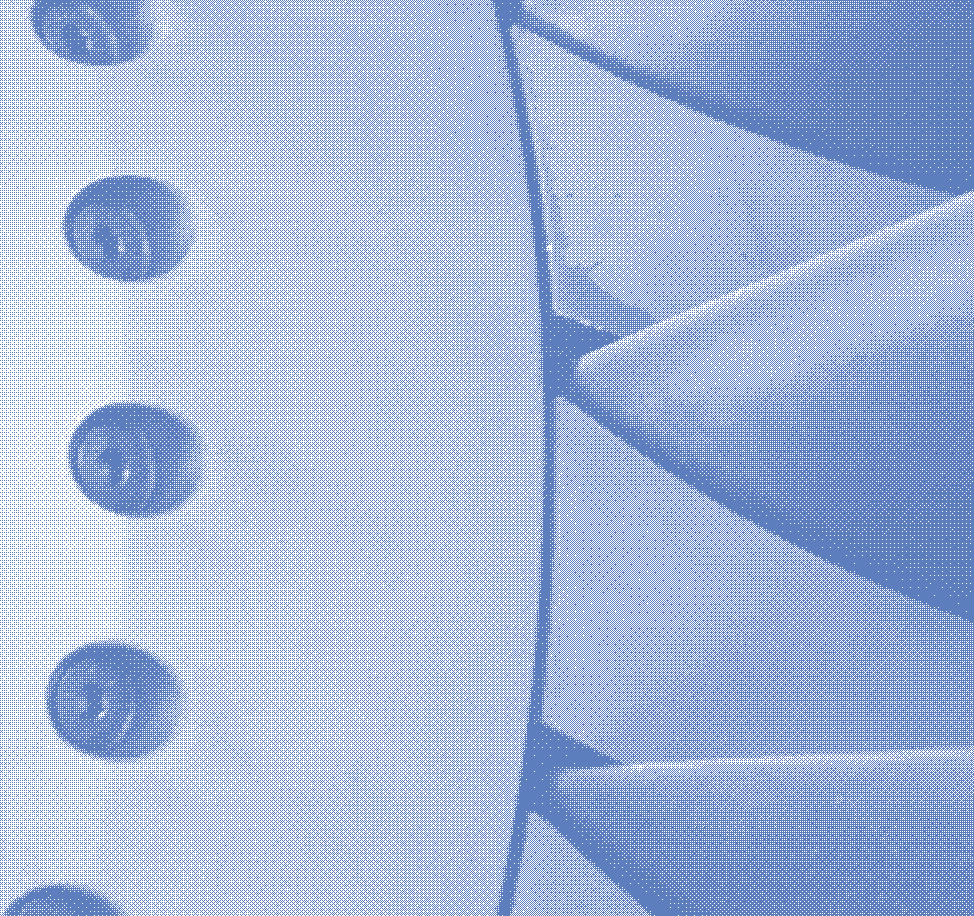
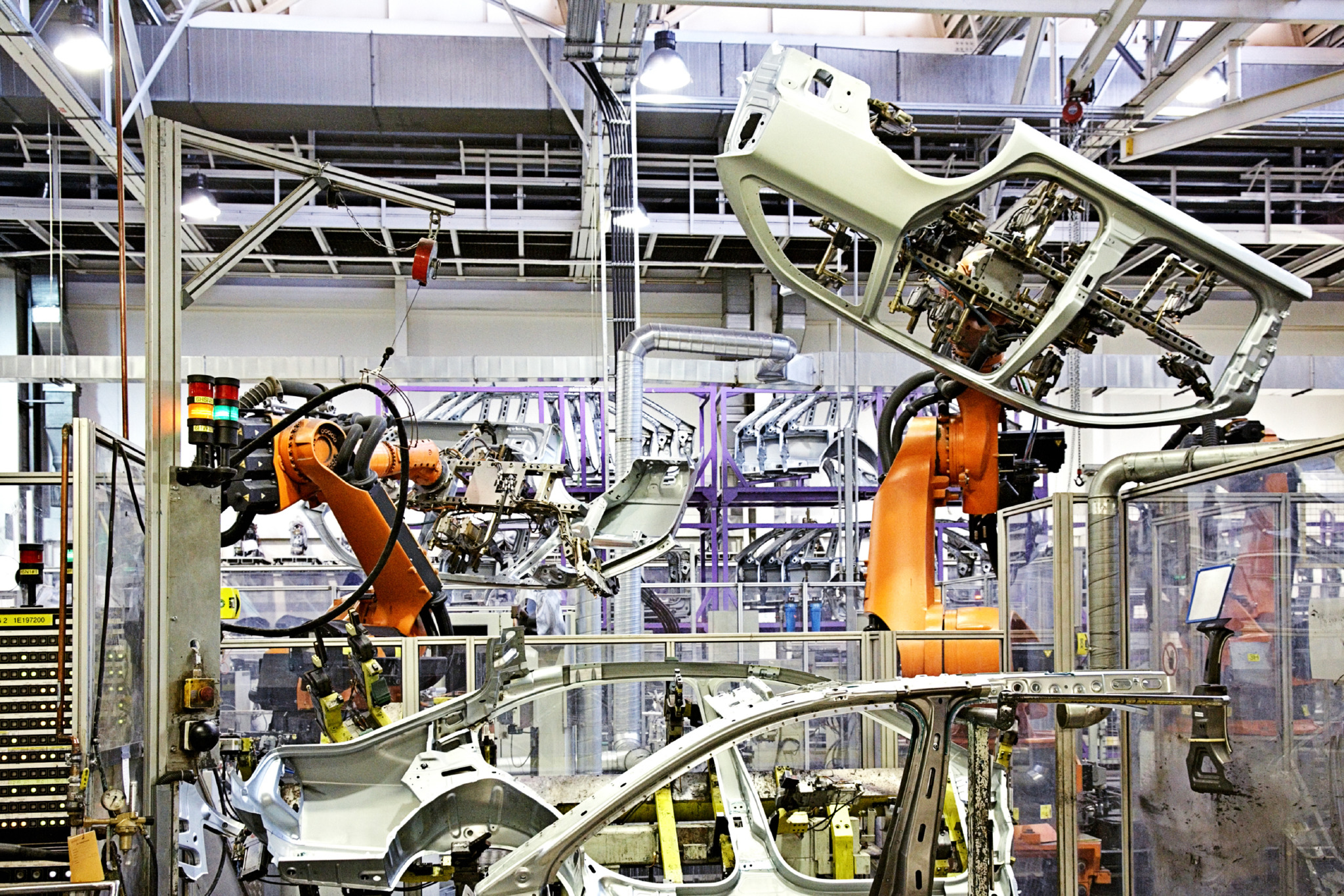
Research Projects
Data and Modelling
Customisable pipeline for understanding formability using virtual materials testing
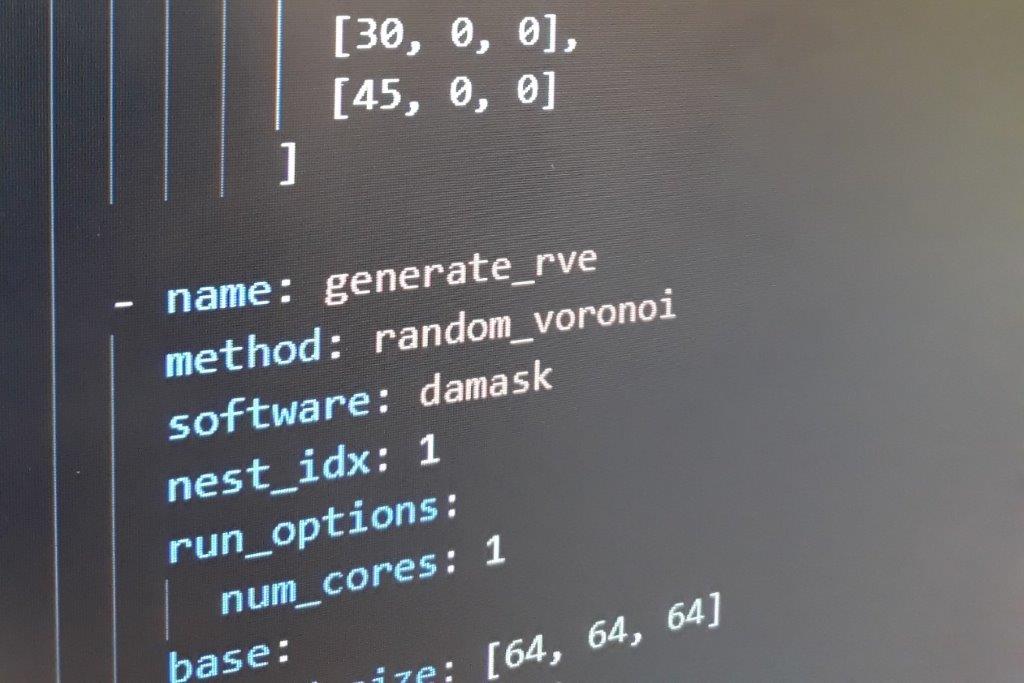
Understanding formability is of vital importance to light alloy component manufacturers. In particular, the mechanical anisotropy of light alloy metals can evolve in complex ways during the forming processes that are necessary for components with precise dimensional requirements. Consequently, it can be difficult to know the final state of the material. An improved understanding of this evolution process would increase manufacturing efficiency and decrease waste associated with meeting quality control thresholds. This is of increasing relevance as manufacturers in the automotive and aerospace industries opt for light alloys to improve, for instance, fuel efficiency. Developing more sophisticated computational modelling methods will assist with this aim.
A range of simulation techniques exist that can provide information at different scales and to varying degrees of precision. For example, we may opt to perform full-field crystal plasticity simulations, which specifically account for the microstructural evolution during deformation. On the other hand, there are many computationally cheaper techniques that can be employed, such as using a simple Taylor model. Currently, for the purpose of improving our understanding of formability, it is not entirely clear where the extra fidelity of the computationally expensive models is most necessary, and where the quick results of a simpler model would suffice.
In this work, we are developing a generalised methodology for predicting mechanical anisotropy in light alloys by efficiently integrating experimental data with materials modelling. Such an approach enables well-informed formability predictions. Specifically, we are interested in finding the best compromise that combines acceptable accuracy with tractable simulations.
We are investigating a number of factors, including: the different ways in which crystal plasticity parameters may be fitted to experimental data; the degree to which simple models such as the Taylor model are able replicate results of full-field models; the prediction of yield surfaces and the forming limit diagrams, and how well different numerical approaches to these compare with data from experiments. We aim to identify, for a given degree of accuracy, what information is most important and what can be safely discarded, since this will improve the confidence with which manufacturers can understand their materials.