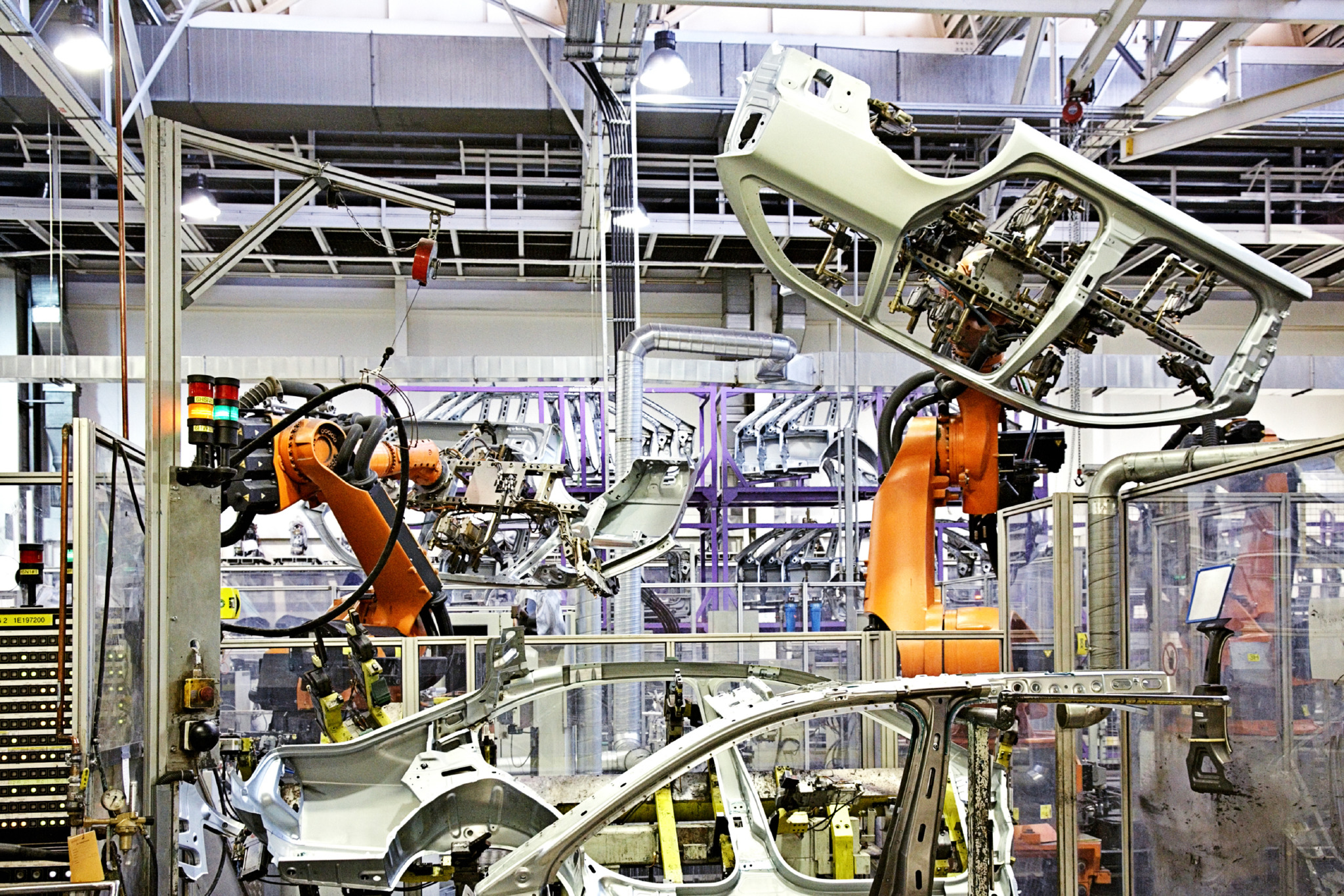
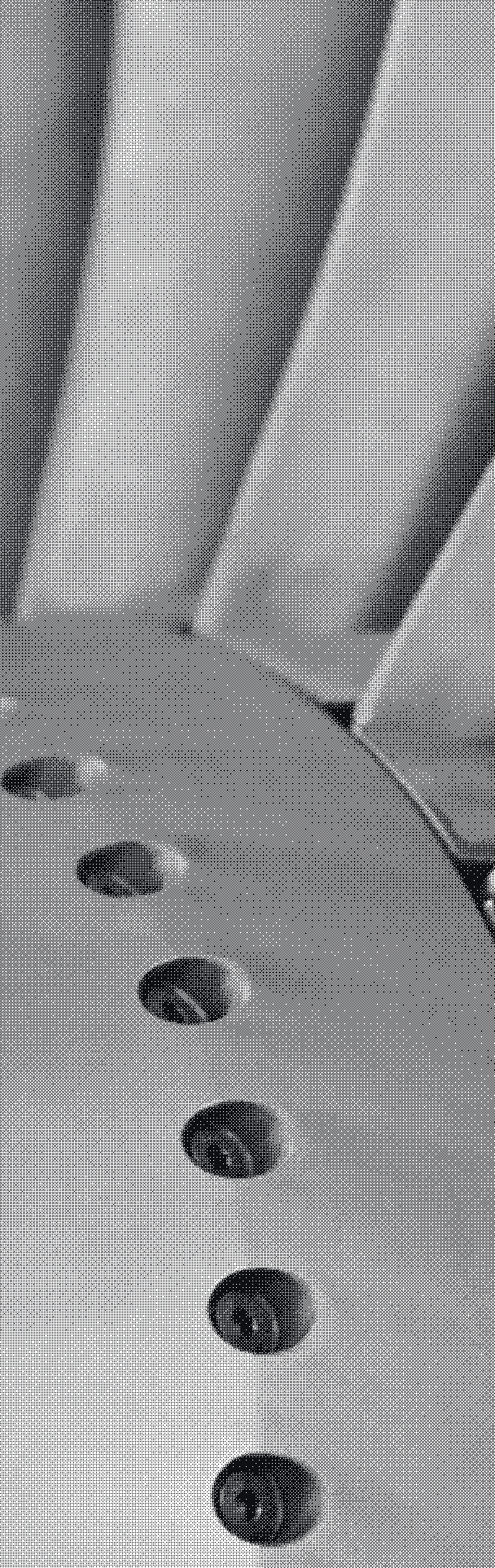
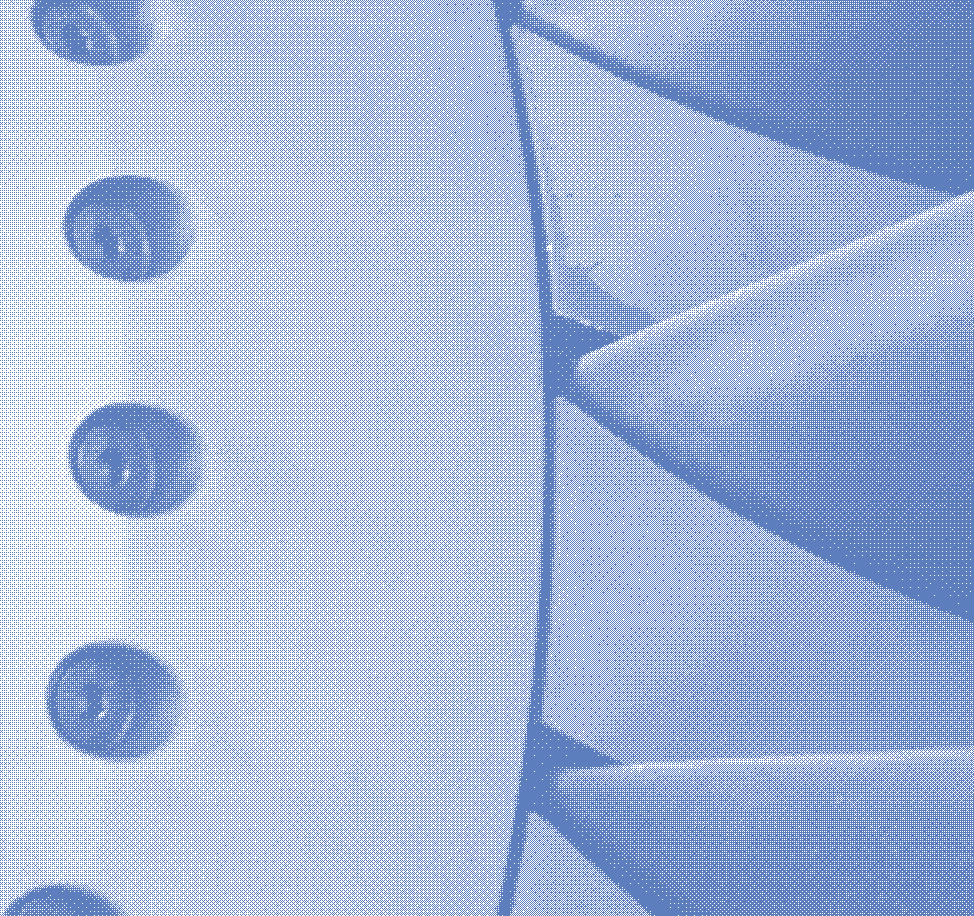
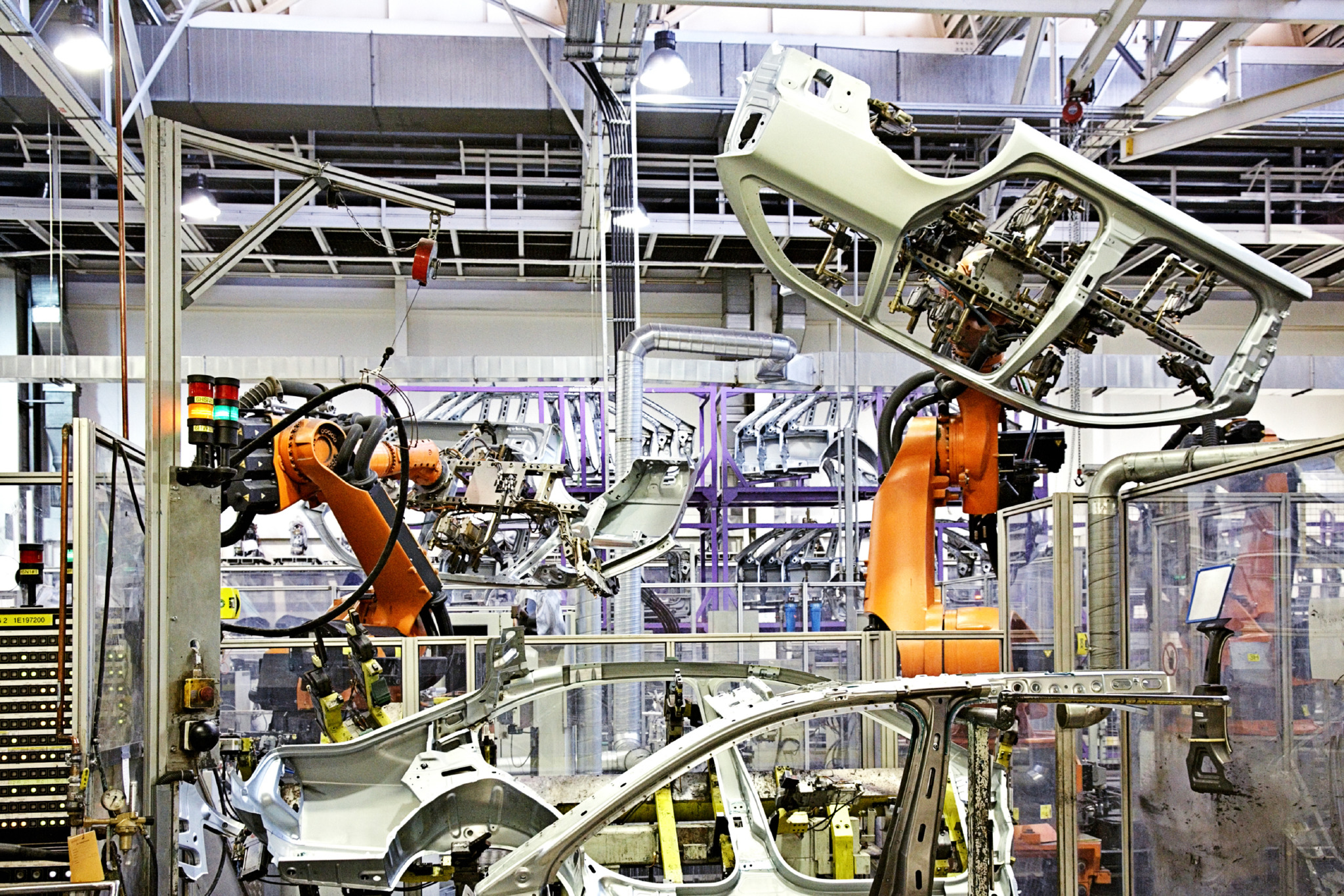
Research Projects
Aluminium
Modelling capabilities of the stress relaxation and creep response occurring within aluminium alloy 2139 during Creep-Age Forming (CAF)
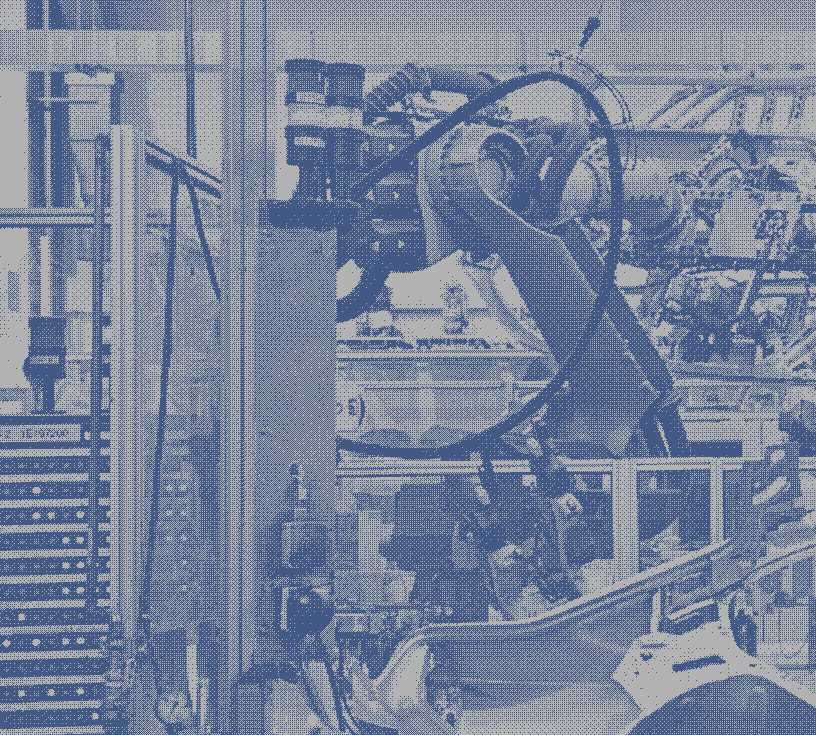
Creep-Age Forming (CAF) as a process has demonstrated significant cost-savings in the aerospace industry in the manufacture of large-scale light alloy panelling. CAF combines the historically separate forming and heat-treatment procedures, into one, thereby reducing processing time, energy and costs. CAF has been successfully used for the manufacture of the top wing skins in the Airbus A380. This research will extrapolate from the wing skin success by developing the forming capabilities into aluminium fuselage components.
Fuselage sheet panelling is initially blast hydro-formed onto die tooling to attain an initial near-net shape form of the final component. CAF is then employed to relieve residual forming stresses, accurately refine the profile through creep/stress relaxation mechanisms and promote artificial age-hardening within the alloy by careful control of process temperatures.
The aim this work is to develop our understanding and modelling capabilities of the stress relaxation and creep response occurring within aluminium alloy 2139 during this process, such that the materials behaviour is better understood and the magnitude of spring back can be accurately predicted to ensure forming tool optimisation.
2139 grade aluminium is a comparatively novel material within the aerospace industry, developed to combine the benefits of 2xxx and 7xxx series together into a strong, tough damage tolerant alloy with improved stress corrosion cracking resistance.