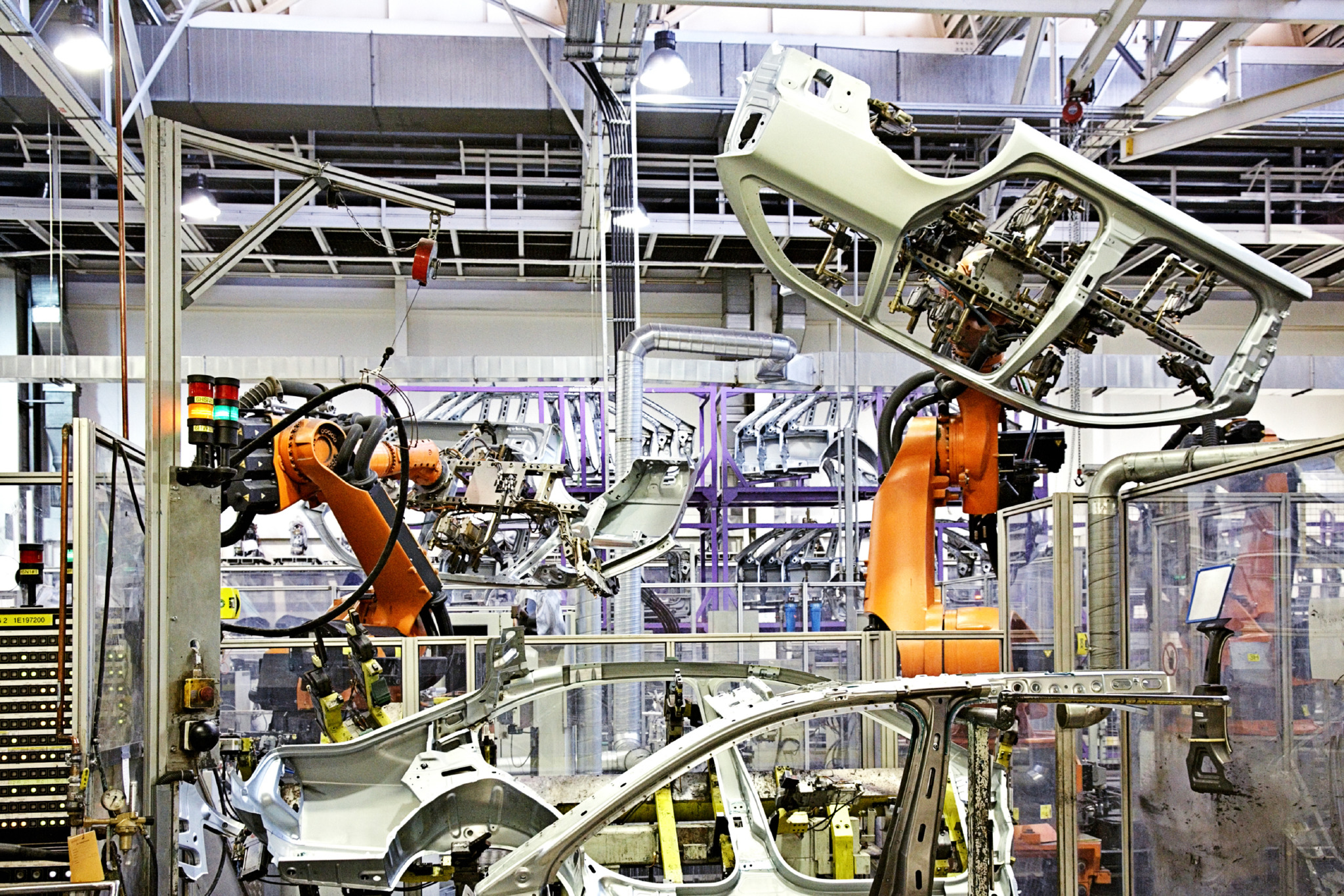
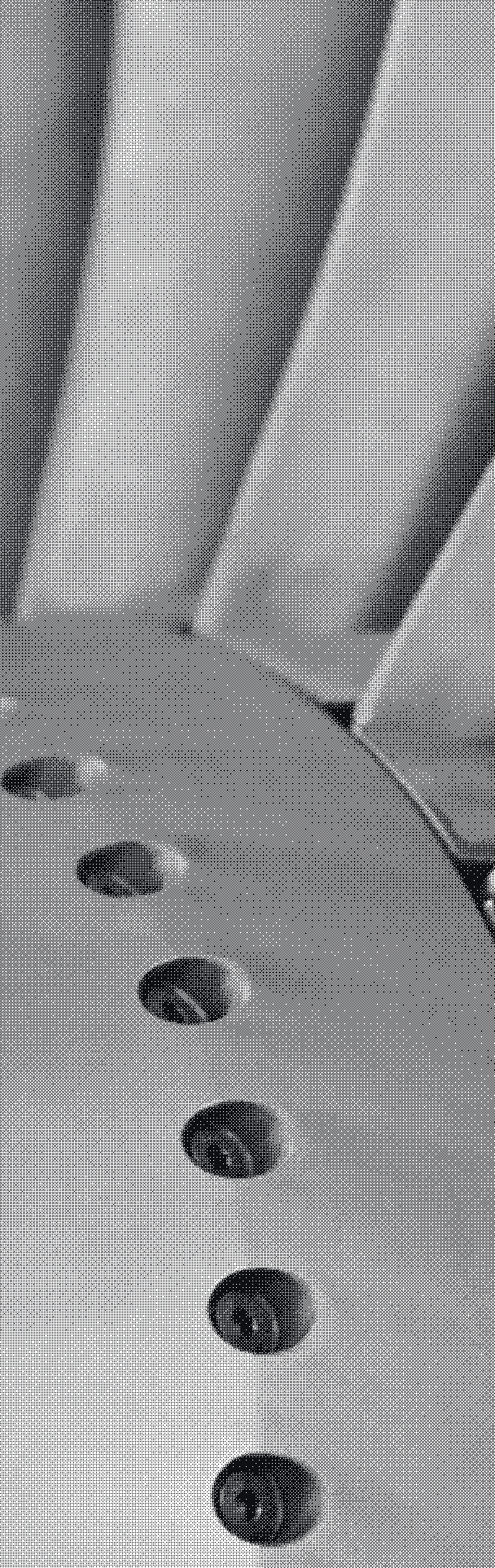
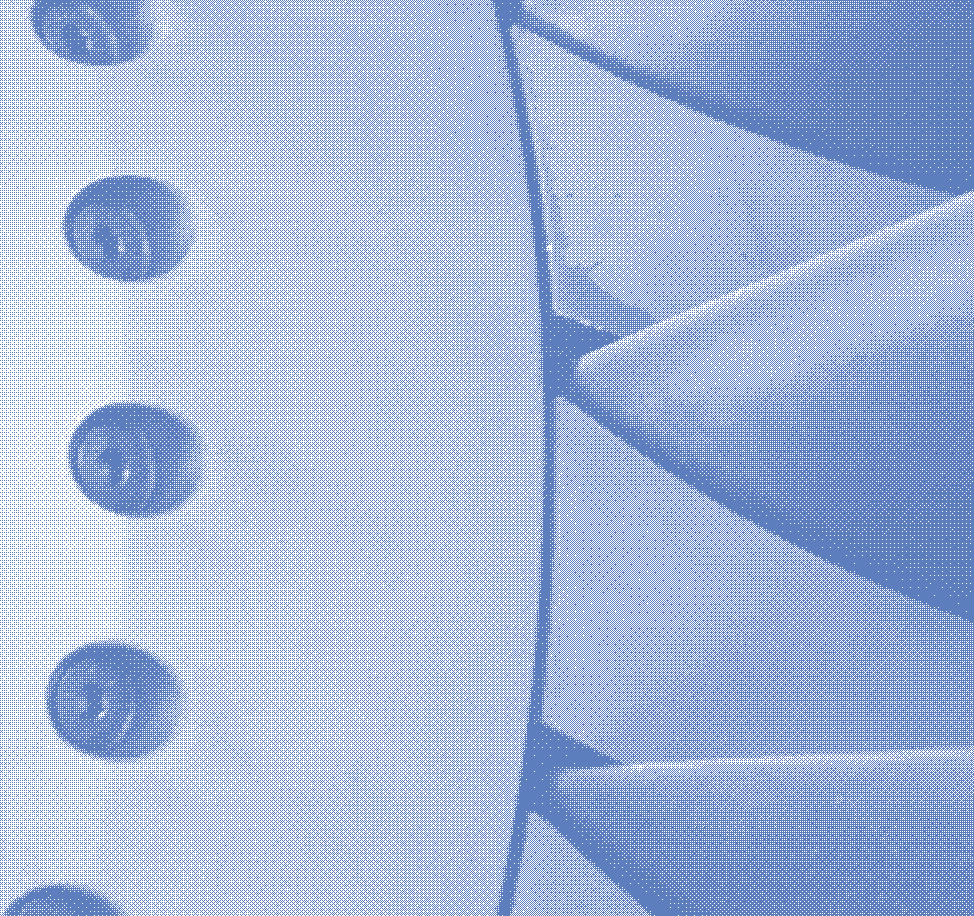
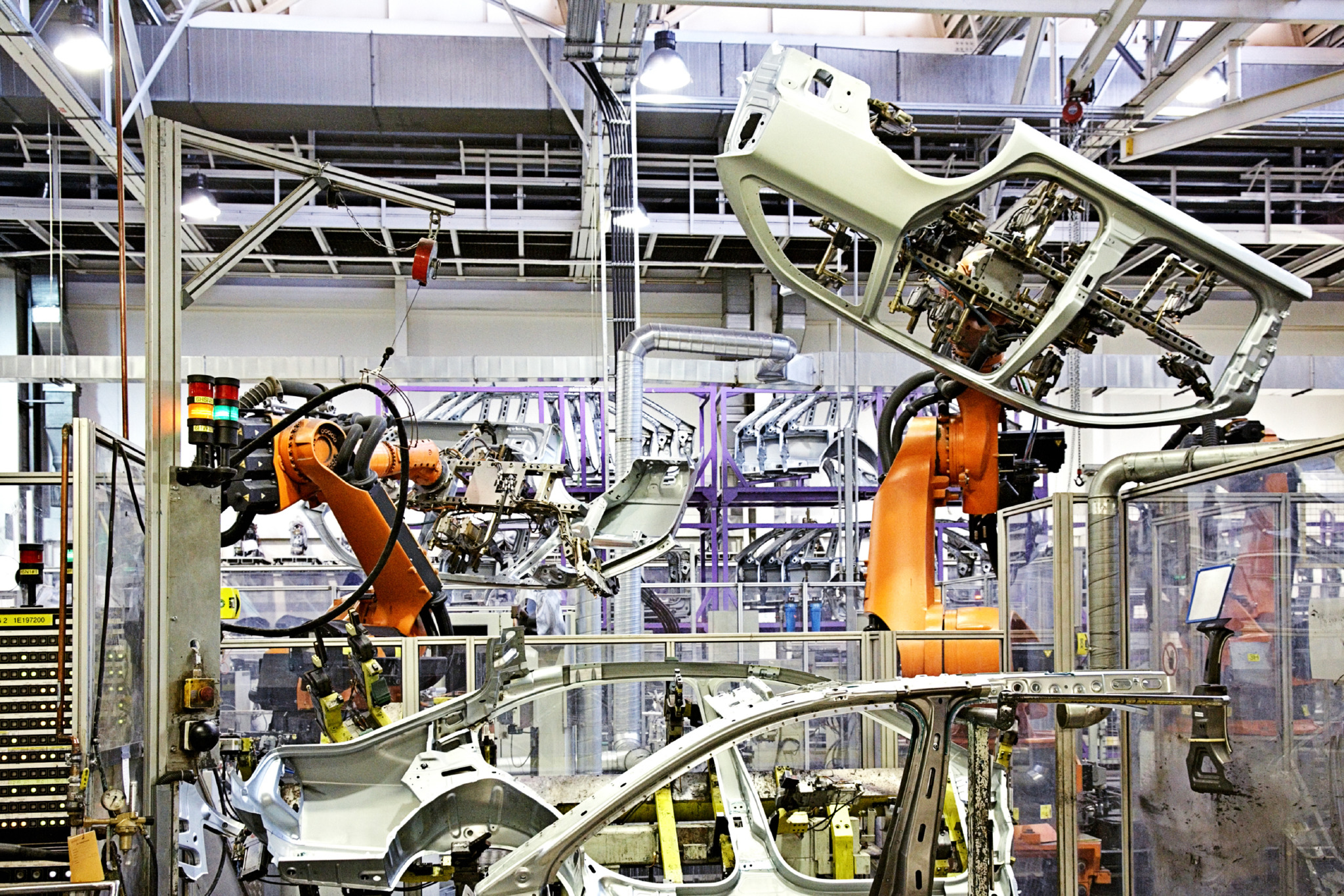
Research Projects
Data and Modelling
Modelling Environmentally Assisted Cracking in Ni-based Superalloys
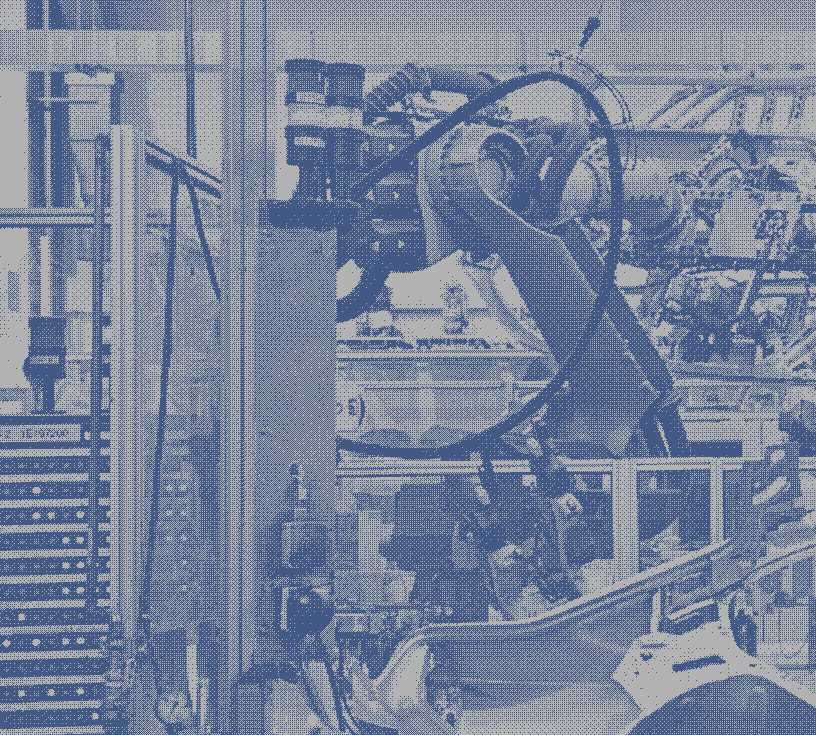
The recent in-service durability of single crystal turbine blades has been far from ideal. Whilst we have the ongoing ‘traditional’ sulphidation issues to manage, a new ‘low’ temperature regime has resulted in blades cracking in locations where stress / temperature combinations would not be expected to nucleate cracks. Loosely termed stress corrosion / corrosion fatigue, the mechanisms are complex and not well understood. This is compounded by limited understanding of the underlying mechanical behaviour with respect to dislocation activity / type and ignorance around the balance of dislocation vs decohesion mediated crack nucleation and growth. Rolls-Royce has to improve its predictive capability in this area. However, it is recognised that this is a complex area with respect to modelling in that there is a requirement to address the evolving stress state, ‘plastic damage’ and ‘environmental degradation’ concurrently. Recent advances in phase field modelling allow a physically informed approach to be taken to address these issues with insightful input from techniques such as Atom Probe Tomography for diffusion rates in regions of high dislocation density etc. This PhD will explore theses new approaches applied to single crystal Ni alloys and, where appropriate, more simple model alloy systems.
Ni-based superalloys are extensively used in aero-engine applications, such as gas-turbine discs or blades, due to their high strength and creep resistance. However, oxygen diffusion into the material at elevated temperatures can lead to a complex failure process known as environmentally-assisted cracking (EAC). With aircraft engine manufacturers driven to increase operating temperatures in excess of 700 oC due to fuel efficiency demands and the need to reduce emissions, EAC in these alloys is becoming increasingly prevalent and is now the major limitation to their use in aero-engine applications. EAC involves many competing mechanical and chemical processes, and a better understanding of these processes is essential to predicting the life of currently used alloys as well as the development of new EAC-resistant materials.
The aim of this PhD project will be to investigate how changes in composition and microstructure affect the susceptibility of Ni-based superalloys to EAC. EAC susceptibility is strongly influenced by the rate of uptake of elemental oxygen, the affinity of the material to form oxides and relaxation mechanisms to accommodate stresses that build up in the material. The student will couple available phase-field models for oxygen diffusion and oxide formation with crystal plasticity models for high-temperature inelastic deformation. Thermodynamic databases, high-temperature mechanical testing data and microstructure characterisation will be available from collaborating research projects in order to determine model parameters and apply the modelling approach to engineering alloys of interest. This modelling approach will then be used to investigate:
- The role of lattice defects, carbides, interfaces and grain boundaries, in determining the transport of elemental oxygen by either acting as trapping sites or low-energy diffusion pathways.
- The microstructural partitioning of alloying elements and their oxide-forming potential, in order to determine preferred microstructural sites for oxide growth.
- Micromechanical driving forces for crack growth, determined by local crystal plasticity, oxygen embrittlement and elastic incompatibility with oxide films.
In particular, this line of investigation will focus on microstructural and compositional differences between standard alloys currently in use and newer alloys in development. The detailed and systematic understanding of EAC mechanisms will then be used by Rolls-Royce, in collaboration with universities like the University of Cambridge, Imperial College London and the University of Birmingham to guide alloy development.