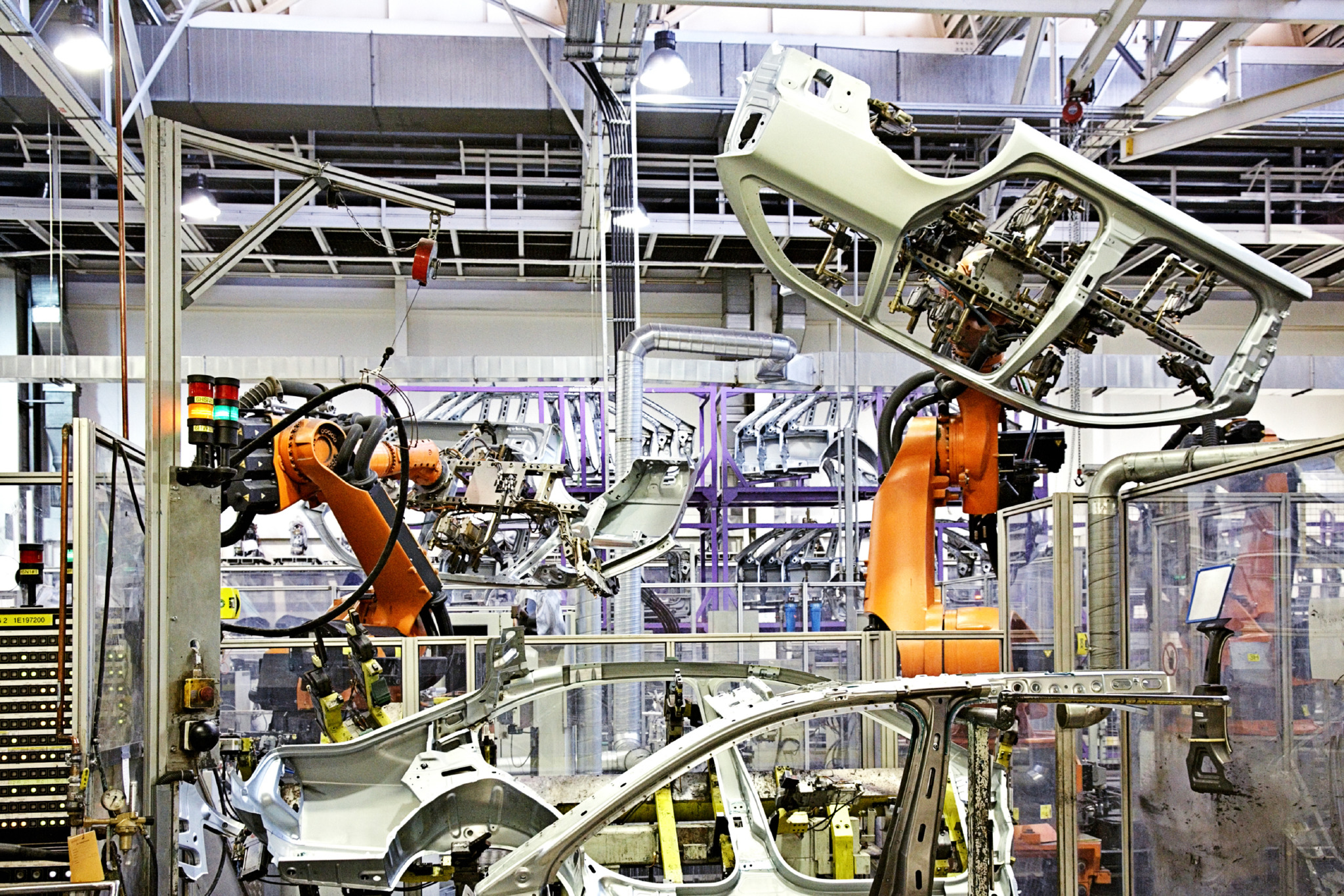
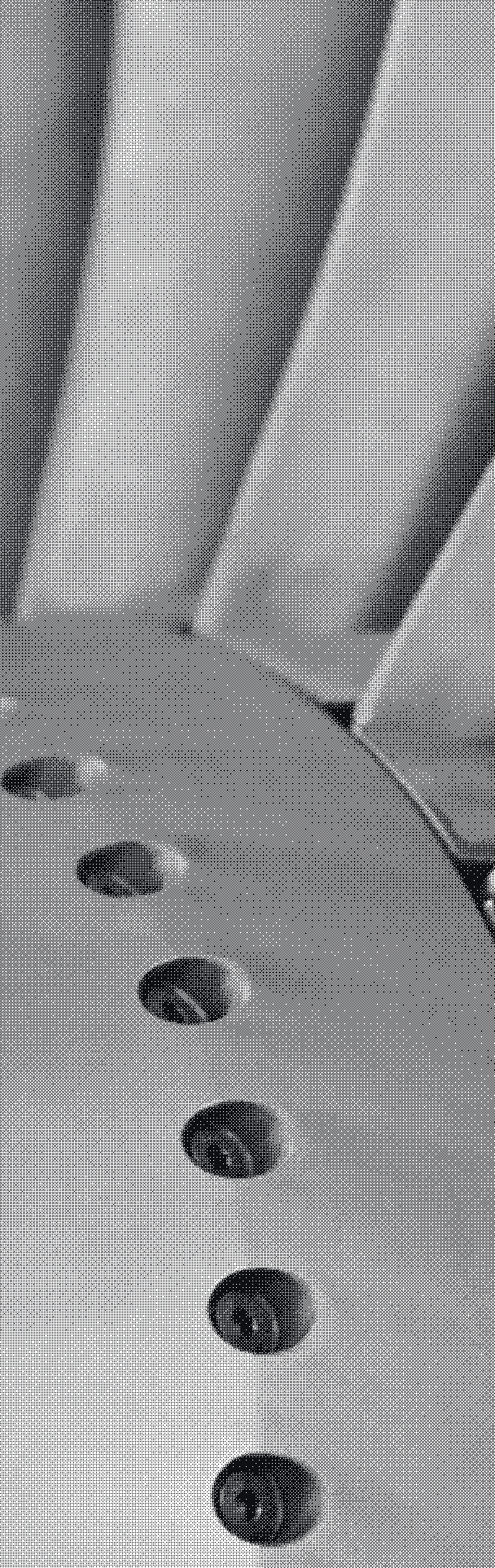
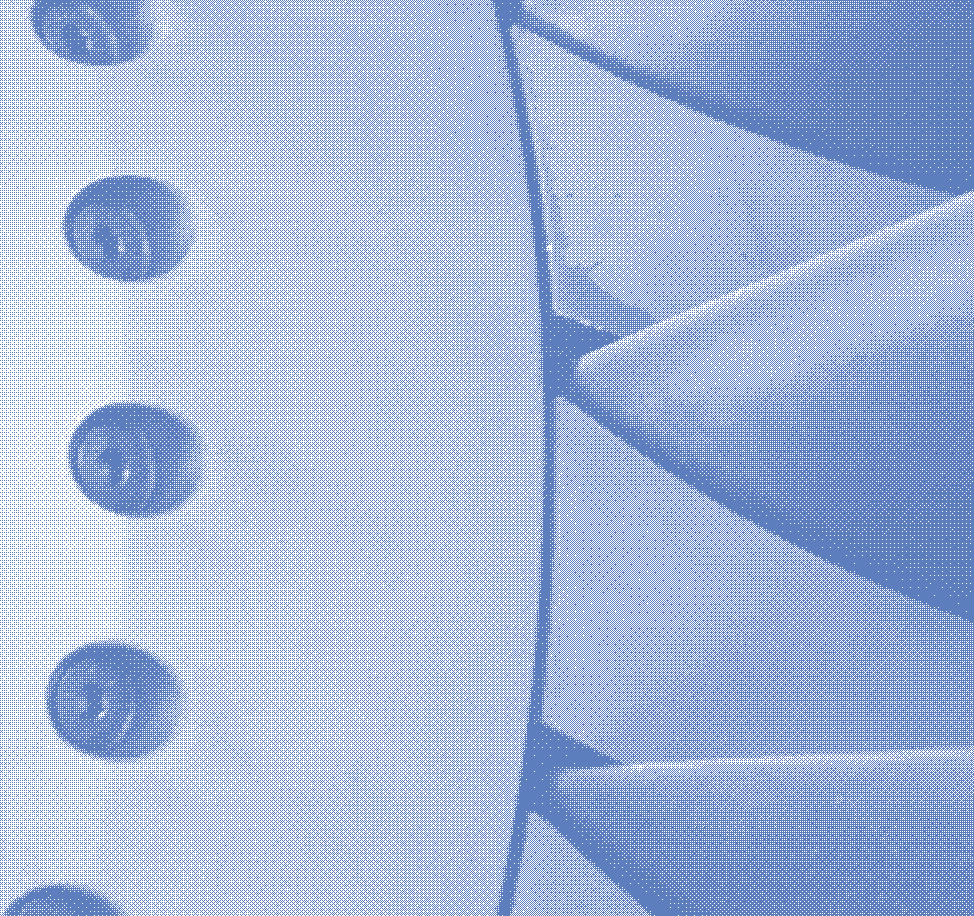
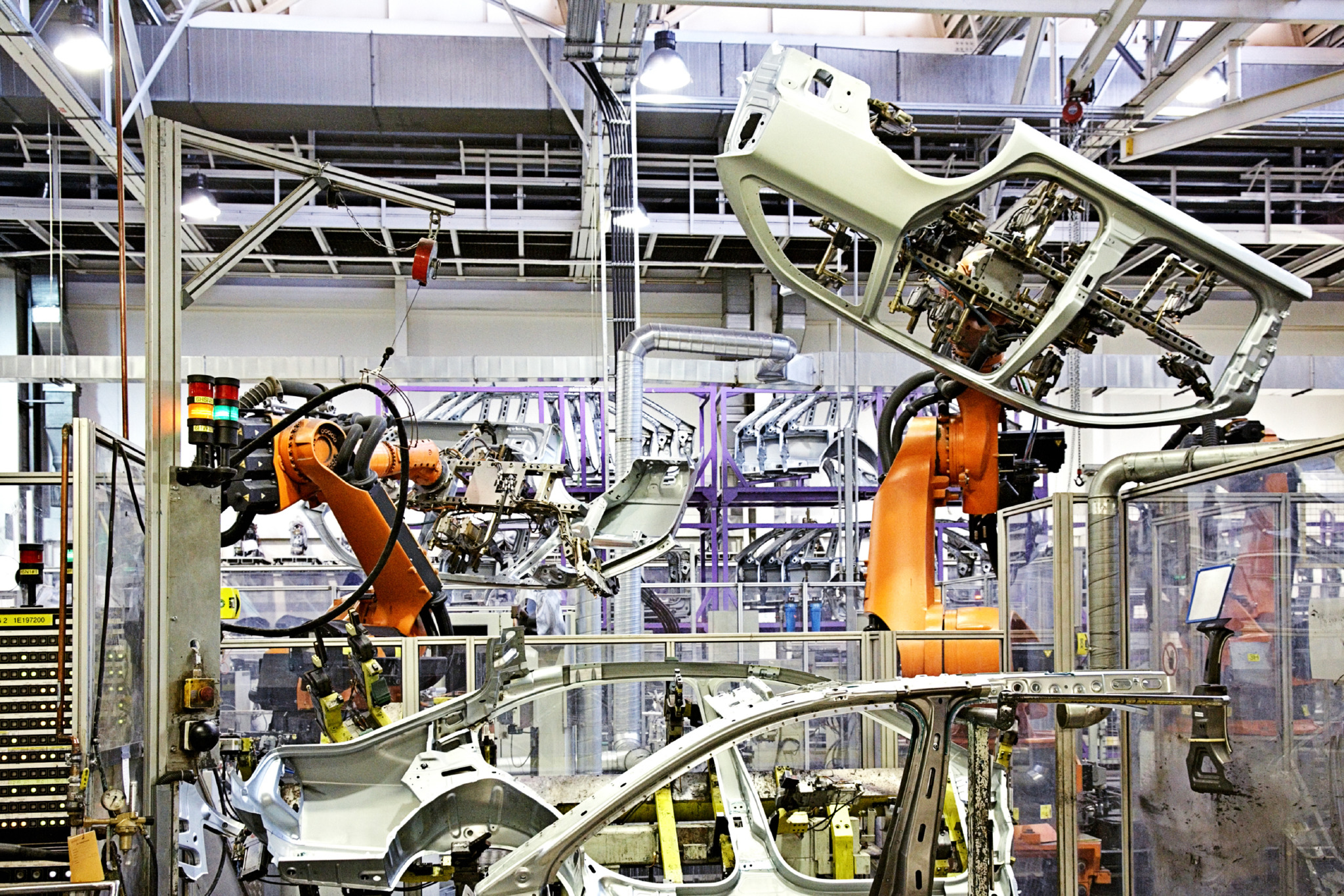
Research Projects
Aluminium / Data and Modelling
Computational formability predictions of Surfalex (AA6016A) with comprehensive characterisation
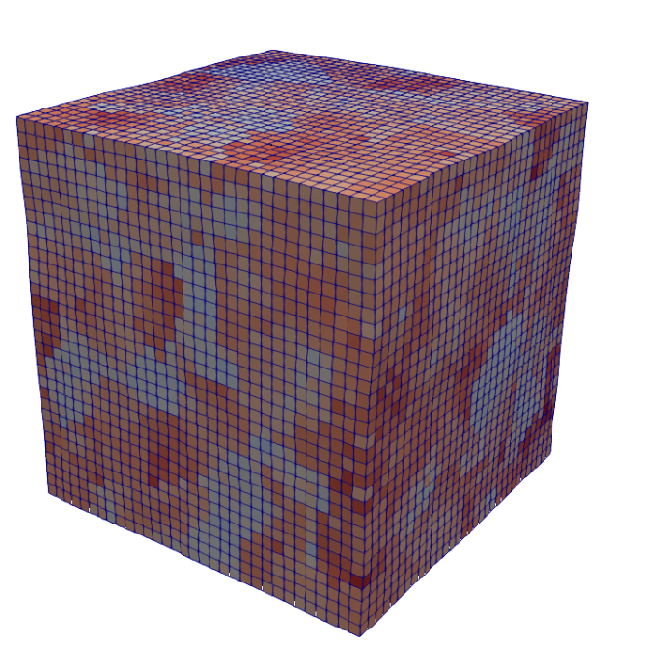
A predictive knowledge of yielding behaviour is critical to improve our understanding of the mechanical anisotropy of light alloys following forming processes. Crystal plasticity (CP) simulations, which explicitly account for the effects of microstructure, enable accurate predictions of yield surfaces, via fitting to various yield criteria. Once yield occurs, the material's stress state remains on the yield surface, but the yield surface itself continues to evolve. An accurate prediction of this evolution will enable more reliable information for manufacturers, whilst limiting the need for difficult or expensive experiments.
Fitting a yield surface to a large set of experimental data is limited by the difficulties of experimentally sampling arbitrary stress states. However, a small set of routine experiments, such as uniaxial tensile tests, can be used to calibrate a larger set of virtual loading tests that are simulated with CP.
In this work, we combine a comprehensive experimental characterisation of an industrially relevant aluminium alloy, Surfalex (AA6016A), with simulated results, as predicted by both full-field CP and Taylor models, to gain a better understanding of the origin of its properties. We particularly focus on investigating formability -- Surfalex has been developed specifically to exhibit high formability and is designed for use as skin in automotive applications. For calibration and comparison, our experimental characterisation of the material includes uniaxial tensile tests with digital image correlation and electron backscatter diffraction analyses. The spectral solver in the software package DAMASK is employed for the CP simulations.
The aims of this work are to combine experimental data with virtual loading tests using CP to predict yield surface evolution and forming limit diagrams, and to compare these with experimental results. In this way, we aim to test the accuracy with which different models can predict the formability of Surfalex.